当前位置:首页 > 文章资讯 > 模具专业 > 汽车注塑产品基础知识及问题分析思路
汽车注塑产品基础知识及问题分析思路
汽车注塑产品使用非常广泛,零部件包含:前后保险杠,仪表板,车门内护板,ABCD柱,主要作用:装饰作用,吸能作用。如存在瑕疵,会影响产品整体美观度,影响顾客体验。
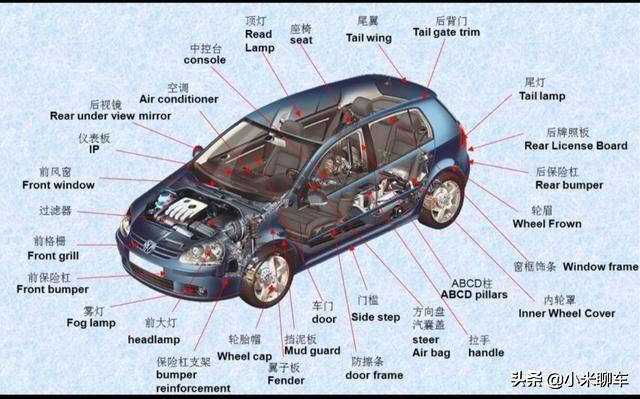
现重点介绍一下汽车塑料知识,产品设计、注塑产品原理及缺陷的改进措施
塑料定义:塑料是以天然或合成树脂为基本原料,在一定的温度和压力下可塑制成型并在常温下能保持其形状不变的材料
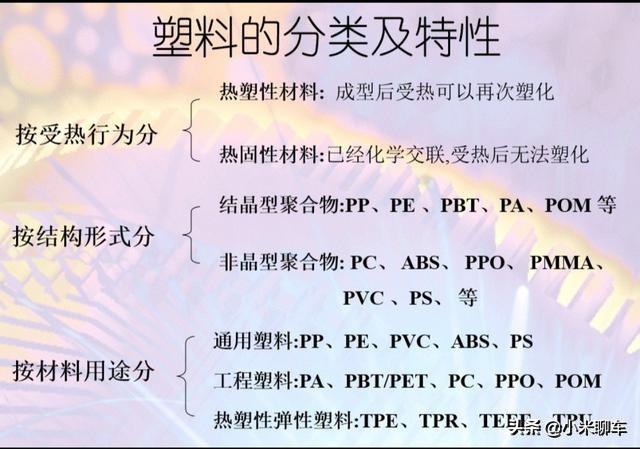
塑料是上世纪才发展起来的一种新型材料,目前世界上的产量已经超过钢铁成为人类使用的四大材料之一。
通常所说的塑料是高分子材料的一种,也可以叫聚合物.塑料的品种很多,性能各具特色,适应范围广泛,发展迅速,直到今天,世界上的新型材料还不断的涌现。
塑料有多种分类方法,可以按受热行为、结构形式、用途等进行分类。塑料通过改性,可以改变塑料的很多性能,主要的改性方法有:填充、增强、增韧、阻燃等,还可以通过共混、共聚等方法制备合金材料。
PE:聚乙烯—结晶性聚合物
PE可以分为HDPE(高密度)、LDPE(低密度)、LLDPE(线性低密度)。
材料特点:PE材料耐溶剂性能好,韧性较高,刚性和硬度较低,耐热性能较差,使用温度较低,耐低温性能好。
主要成型加工方式:注塑、挤出、吹塑等
主要用途:一般塑料件、吹塑产品、管材等
燃烧特性:PE具有易燃性,不会自然熄灭,燃烧过程中有石油气味产生。
PP:聚丙烯—结晶性聚合物
PP可以分为均聚丙稀和共聚丙稀2个大类,性能的主要区别是均聚丙稀的刚性、耐热性能、透明性等较好,共聚丙稀的韧性、加工性能较好。
材料特点:PP材料质量轻,耐溶剂性能好,刚性比PE好,耐热性能较好,但耐 候性能较差,在0℃以下易变脆。可以通过多种改性方法制备复合材料,改性后性能相差很大。
主要成型加工方式:注塑、挤出、吹塑、流延、双向拉伸等,容易成型
主要用途:种类繁多,在汽车上面的应用极为广泛。
燃烧特性:PP具有易燃性,不会自然熄灭,燃烧过程中有特殊味道(柴油气味)产生。
ABS:丙稀腈-丁二烯-苯乙烯三元共聚物—非晶型聚合物
ABS具有卓越的综合性能,其主要有点如下:
良好的光泽、流动性、低的收缩率、容易成型,容易着色、较好的刚性
缺点:材料耐候性不好,易变色,耐热温度不高。通过改性,可以改善。
目前市场上有较多的新型ABS材料:AES、ASA、MBS、透明ABS等
主要成型加工方式:注塑、挤出等,容易成型
主要用途:种类繁多,在汽车上面的应用极为广泛。
燃烧特性:ABS具有易燃性,不会自然熄灭,燃烧过程中有橡胶气味、辣味产生。
PVC:聚氯乙稀—非晶型聚合物
PVC的性能特点:易分解,必须加入稳定剂。其他助剂:润滑剂、增塑剂等
软PVC、硬PVC、PVC型材、PVC人造革薄膜
由于PVC材料具有良好的手感和花纹成型性且材料成本低等优点,因此目前PVC搪塑仍是使用最广的仪表板表皮加工工艺,PVC粉料占据了搪塑成型工艺的绝大部分市场。由于PVC 材料的玻璃化温度较高,材料在低温环境下发脆,易造成无缝气囊仪表板在低温状态爆破时,气囊区域PVC表皮碎裂而飞出,对乘客产生安全隐患,PVC在抗老化性、增塑剂迁移等方面也存在问题,因此出于安全及环保原因,目前各主机、饰件及材料生产厂商相继开发出了PVC的替代材料及工艺。
燃烧特性:PVC具有难燃烧性,会自然熄灭,燃烧过程中有氯气味产生。
PA:聚酰胺(尼龙)—结晶型聚合物
PA是广泛使用的材料之一,主要使用的材料由2大类:PA6、PA66
其中PA66的强度和刚性比PA6要好,但韧性相对较差。
尼龙通过增强、增韧、填充、阻燃等改性,可以制备出很多种类的产品,满足各种需求。通过增强的尼龙如PA66加入30%的玻璃纤维,一般可以将其特征标识为PA66-GF30。增韧的产品最著名的是Dupont公司的ST801,填充和阻燃产品主要用在电子电器类产品里较多。
PA除了PA6、PA66外还有很多特种PA:
PA46:耐热性能特高,熔融温度达到290℃以上,HDT达到190℃,增强GF30后, HDT达到280℃以上。在汽车发动机、变速器等领域有较多使用PA1010:具有高度延伸性,拉伸时能使分子定向,使其强度提高,优良耐化学品性PA12:吸水率低,柔韧性好。挤出制品可以制作各种油管、软管等
透明PA:无定形材料,透明性可以比PC更好
其他类型:PA612、PA11、PA13、PA9、PA4、PA7、PA8、PA9等
MC (单体浇铸)尼龙、RIM(反应注射成型)尼龙
各种尼龙因为结构不一样,性能有极大的差别。
燃烧特性:PA具有不易燃烧性,会自然熄灭,燃烧过程中有烧羊毛、烧指甲味产生。
对塑料进行性能测试,评价塑料性能的优劣,主要有以下一些方法:
1.力学性能:拉伸(屈服)强度、断裂伸长率、弯曲强度、弯曲模量、硬度、冲击强度、蠕变和应力松弛等
2.热 性 能:耐热性、耐寒性、维卡软化点、热变形温度(HDT)、熔点、最高连续使用温度、脆化温度
3.电 性 能:体积电阻率、耐电弧性能
4.光学性能:透光率、雾度
5.化学性能:耐化学品性、耐溶剂性能、耐环境应力开裂
6.耐自然老化性能:大气自然老化、紫外光加速老化、氙灯加速老化、抗菌试验
7.耐燃烧性能:燃烧速度
8.固有特性:密度、收缩率、吸水性、熔融指数(MI)
9.其他性能:油漆粘附力、耐渗透性等
汽车上使用的材料越来越多,有报道称:汽车中使用塑料的重量比达到22%,也称报道有全塑汽车设计成功。塑料因其比重小、节能、易成型、设计灵活、美观和环保等有点,得到越来越多的应用。
汽车塑料的一般要求:
1.耐热性:一般要求在90℃以上,有些部件要求135 ℃甚至200 ℃以上
2.耐候性:一般的外饰件、光线直接照射的内饰件有较高要求
3.冲击韧性:保险杆、紧固件、内饰件等都有较高要求
4.材料刚性:除弹性材料外一般都有要求
5.燃烧性:汽车材料一般都有阻燃要求,但一般较低
6.低温性:较多汽车材料有耐低温要求
7.材料弹性:要求弹性体材料如拨钮、门窗密封条、风挡等
8.气味性:塑料如POM有较大的气味
9.硬度:塑料的重要指标
10.其他特性:涂装性、光泽度、颜色、有害物质含量等
五、塑料件的设计前提
1、在设计前,首先应查找公司和同行类似的产品,原有的产品发生过哪些问题,有哪些不足,参考现有的成熟结构,避免有问题的结构形式。
2、从造型图和效果图理解造型风格,配合产品的功能分解,确定零件折分的数目(不同的表面状态要么分为不同的零件,要么在不同的表面之间须有过度处理),确定零件表面间的过度处理,决定零件之间的连接方式,零件之间的配合间隙。
3、零件强度与连接强度的确定
根据产品大小,确定零件主体壁厚。零件本身的强度,由壁厚,结构形式(平板形状的塑料件强度最差),加强筋与加强骨共同决定。在决定零件的单个强度的同时,须确定零件之间的连接强度,改变连接强度的方法有,加螺钉柱、加止口、加扣位。
六、塑料件的设计要点
利用注塑工艺生产产品时,由于塑料在模腔中的不均匀冷却和不均匀收缩以及产品结构设计的不合理,容易引起产品的各种缺陷:缩印、熔接痕、气孔、变形、拉毛、顶伤、飞边。
为得到高质量的注塑产品,我们必须在设计产品时充分考虑其结构工艺性,下面结合注塑产品的主要结构特点分析避免注塑缺陷的方法。
1、开模方向和分型线
每个注塑产品在开始设计时首先要确定其开模方向和分型线,以保证尽可能减少抽芯机构和消除分型线对外观的影响。
1.1开模方向确定后,产品的加强筋、卡扣、凸起等机构尽可能设计成与开模方向一致,以避免抽芯,减少拼缝线,提高外观质量,延长模具寿命。
1.2 例如:保险杠的开模方向一般为车身坐标X方向,如果开模方向设计成与X轴不一致,则必须在产品图中注明其夹角。
1.3 开模方向确定后,可选择适当的分型线,以改善外观及性能。
2、脱模斜度
2.1 适当的脱模斜度可避免产品拉毛。光滑表面的脱模斜度应大于0.5度,细皮纹表面大于1度,粗皮纹大于1.5度。
2.2 收缩率大的制件选用较大的脱模斜度;对于大尺寸制件或尺寸要求高的制件采用较小的脱模斜度。
2.3 适当的脱模斜度可避免产品顶伤。
2.4 一般情况下脱模斜度不包括在制件公差范围内。
3、产品壁厚
3.1 应尽量壁厚均匀、厚度适当、不应有突变,厚度不同时应逐渐过度。
3.2 各种塑料均有一定的壁厚范围,一般0.5~4mm,当壁厚超过4mm时,将引起冷却时间过长,产生缩印等问题,应考虑改变产品结构。满足要求时尽量减小壁厚。
3.3 壁厚不均会引起表面缩印。如PP、POM、PE、PA更为显著。
4、加强筋
4.1 加强筋的合理应用,可增加产品刚性,减少变形。
4.2 加强筋的厚度必须小于产品壁厚的1/3,否则引起表面缩印。
4.3 加强筋的单面斜度应大于1.5度,以避免顶伤。
4.4 多条加强筋相互错开、布置得当,之间的距离大于4t;筋的高度低于3t,不易过大,否则会使筋部受力破损。
4.5 螺钉柱子的筋取至少低于柱子端面1mm,筋至少需要低于零件表面或分型面1mm,。
4.6 设置方向应与槽内料流方向一致,避免料流干扰而损害产品的质量。
5、圆角
5.1 圆角太小可能引起产品应力集中,导致产品开裂。
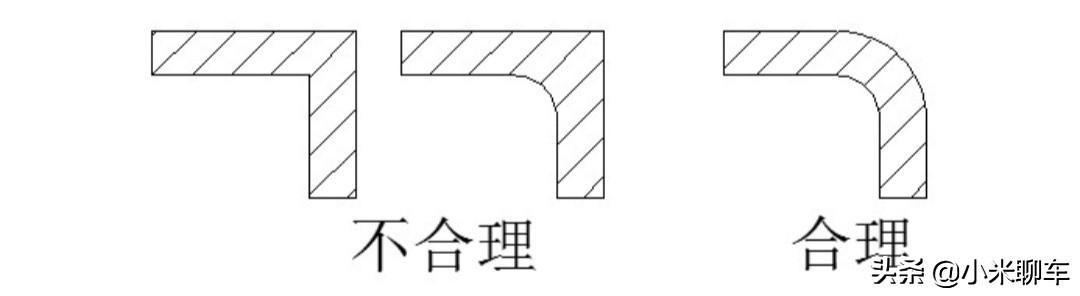
5.2 圆角太小可能引起模具型腔应力集中,导致型腔开裂。
5.3 设置合理的圆角,可以提高制件强度,有利于充模和脱模,还可以改善模具的加工工艺,如型腔可直接用R刀铣加工,而避免低效率的电加工。
5.4 注塑圆角值由相临的壁厚决定,一般为0.5~1.5t,但不小于0.5mm。
5.5 不同的圆角可能会引起分型线的移动,应结合实际情况选择不同的圆角或倾角。
6、孔(通孔、盲孔、螺纹孔等)
6.1 孔的形状应尽量简单,一般取圆形。
6.1 应尽量设计在不减弱强度的部位。
6.2 孔的轴向和开模方向一致,可以避免抽芯。
6.3 当孔的长径比大于2时,应设置脱模斜度。此时孔的直径应按小径尺寸(最大实体尺寸)计算。
6.4 盲孔的长径比一般不超过4。
6.5 孔与产品的边缘的距离一般大于孔径尺寸。
7、注塑模的抽芯机构及避免
7.1 当塑件按开模方向不能顺利脱模时,应设计抽芯机构,抽芯机构能成型复杂产品结构。
但是易产生产品拼缝线,缩印等缺陷,并增加模具成本、缩短模具寿命。
7.2 设计注塑产品时,如无特殊要求,尽量避免抽芯结构。如孔轴向和筋的方向改为开模方向,利用型腔型芯碰穿等方法。
8、一体铰链
8.1 利用PP料的韧性,可将铰链设计成和产品一体。
8.2 作为铰链的薄膜尺寸应小于0.5mm,且保持均匀。
8.3 注塑一体铰链时,浇口只能设计在铰链的某一侧。
9、嵌件
9.1 在注塑产品中镶入嵌件可增加局部强度,硬度,尺寸精度 和设置小螺纹孔(轴),满足各种特殊需求,同时会增加产品成本。
9.2 嵌件一般为铜,也可以是其它金属或塑料件。
9.3 嵌件在嵌入塑料中的部分应设计止转和防拔出结构。如: 滚花、孔、折弯、压扁、肩等。
9.4 嵌件周围塑料应适当加厚,以防止塑件应力开裂。
9.5 设计嵌件时,应充分考虑其在模具中的定位方式(孔、销、磁性)
10、标识
产品标识一般设置在产品内表面较平坦处,并采用凸起形式,选择法向与开模方向尽可能一致的面处设置标识,可以避免拉伤。
11、注塑件精度和表面粗糙度
11.1 由于注塑时收缩率的不均匀和不确定性,注塑件精度明显低于金属件,应按标准选择适当的公差要求(SJ/T 10628—1995)。
11.2 蚀纹表面不能标注的粗糙度。在表面光洁度特别高的地方,将此范围圈出标注表面状态为镜面。
11.3 塑料零件的表面一般平滑、光亮,表面粗糙度一般为Ra2.5~0.2um.。
12、注塑件的变形
提高注塑产品结构的刚性,减少变形,尽量避免平板结构,合理设置翻边,凹凸结构。设置合理的加强筋。
13、气辅注塑
13.1 采用气辅注塑,可提高产品刚性,减少变形。
13.1 采用气辅注塑,可以避免缩印。
13.2 采用气辅注塑,可以节省原料,缩短冷却时间。
14、焊接(热板焊、超声波焊、振动摩擦焊)
14.1 采用焊接,可提高联接强度。
14.2 采用焊接,可简化产品设计。
模具制造常见问题
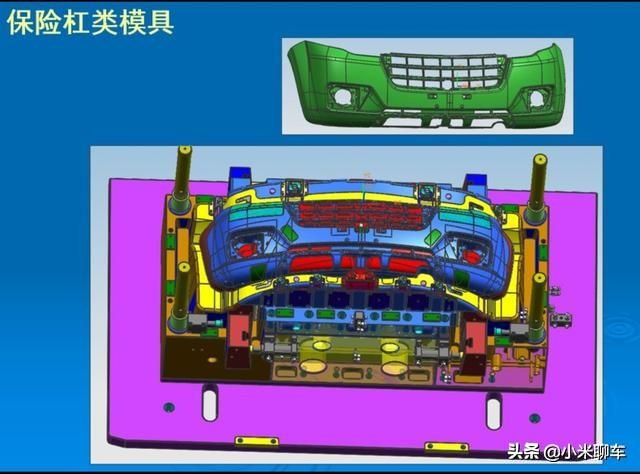
1.数据分析确定
①外观线条顺畅 ②装配结构和脱模斜度合理
③分型线选择 ④浇口位置 ⑤产品厚度变化
⑥产品成型问题预测
2.模具结构设计
①分型线选择和分型面设计 ②产品取出性 ③浇口位置,大小,形式选择 ④成型注塑机参数 ⑤产品模穴数和布局 ⑥确定主要成型零部件形状 ⑦产品成型问题预测和设计更改预留量
注塑过程中的问题及解决方案:
1、 虎皮纹:定义:制件表面上呈现的虎皮花纹状的圆弧形条纹,一般间距较大
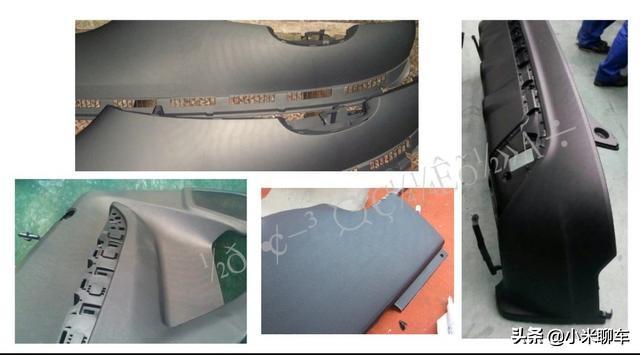
3、 条纹呈周期性变化的明暗交替;
4、 条纹大致垂直于熔体的流动方向;
5、 条纹分为亮区和暗区,亮区的光泽度高,暗区的光泽度差;
6、 如果制件的正面是亮区,则背面是暗区,两者交替出现;
虎皮纹的产生源于塑料熔体充模的不稳定流动。一般会出现在离浇口的远端,在薄壁、流程长的产品中容易出现。 虎皮纹的产生机理
选用适当的产品壁厚;
薄壁化是目前汽车注塑件的发展趋势,虎皮纹问题将会越来越严重;
渐变的壁厚设计;
产品设计上的解决方案
增加浇口数量,减少流程比;
增加流道直径,扩大浇口的厚度和宽度;
优先采用直浇口和扇形浇口,避免采用潜伏式浇口和点浇口;
熔接痕:
根据moldflow的分析标准,当熔接线汇合角>135°时,熔接线可以称之为熔合线,此时熔接线不易看到,强度很高;
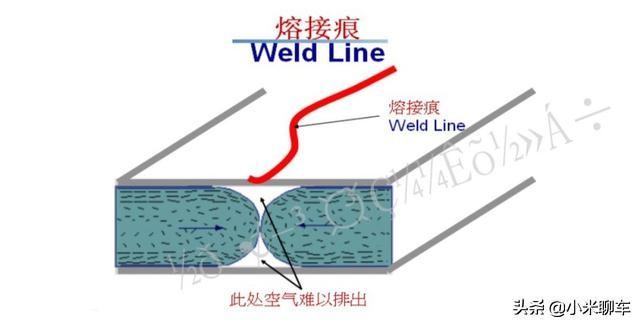
当熔接线汇合角<135°时,熔接线称之为缝合线,此时熔接线比较清晰,如果该汇合角>75°,熔接线虽然比较清晰,但是强度较高,通过处理,喷漆可以遮盖住;
如果熔接线汇合角<75°,熔接线即使经过处理,喷漆也无法遮盖,而且熔接线的强度较差。
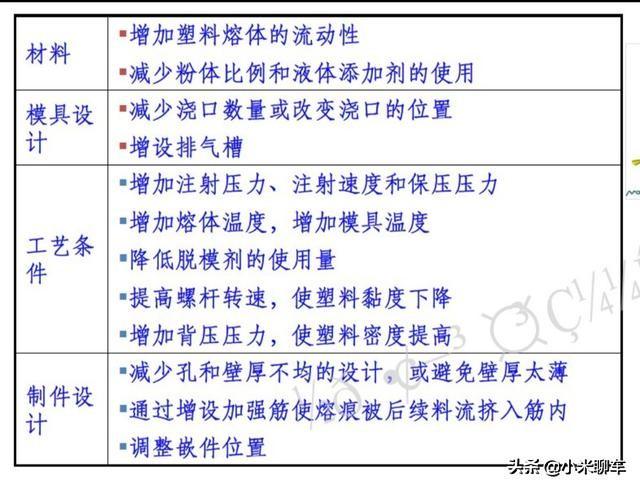
-熔接痕色差 Weld Lines 定义:经常碰到制件的表面在熔接线两侧光泽、颜色鲜艳度或者色泽明显的区别,我们将这一类问题统称为熔接线色差。熔接线还是属于较易解决的缺陷,更难解决的是熔接线色差,如图所示为门板熔接线色差的情况,这时需要材料和模具做较大配合才能解决,工艺上也要采用较大变动。
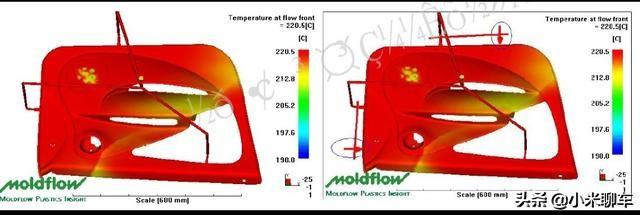
这是一张流动前沿的温度分布图,我们可以清晰地发现,在上面的两个浇口与最下面的那个浇口进胶熔体的熔接位置,存在明显的温度差,该温度差高达8-14度,温度差异过大,虽然熔接线依然在较高的温度熔接,而且熔接线强度问题不大,但是却导致熔接位置光泽差异明显,使熔接线清晰可见。
•此外,对于温度下降较多的一侧,主要是因为流动截面突然增大或者与对面来胶截面差异大,导致熔体流速差异明显,流速慢的一侧与模具的热交换多,温降大,固化层或冷胶层多,流动阻力大,因此易于形成波浪状流痕,针对该制件,因为热流道,改浇口位置难度较大,我们建议增加两个浇口,如下图:
辅助CAE分析,合理布置浇口位置;
浇口宽度设计合理,流动阻力小,增加工艺窗口;
工艺配合,调整顺序阀开启顺序,增加料温和模温;
调整对应浇口的热流道问题,避免出现温差线;
模具加强排气,必要时设计排气镶件;
材料配合;
尺寸不合格:
制件的尺寸取决于以下几个方面
1.材料的收缩率
2.制件的结构设计
3.模具的收缩率
4.热膨胀系数
5.产品的成型周期
6.成型工艺
尺寸不匹配的原因
-目前收缩率测试方法没有统一的标准,各个厂家如巴塞尔、北欧等都使用自己的测试方法。 金发的材料收缩率测试方法 尺寸不匹配的原因 -41-
注塑收缩率:收缩率样板注塑完后,在标准状态下(实验室恒温恒湿)放置6h以上,测量收缩率板的距离。
烘烤后收缩率:将测完的样板80℃烘烤2h后,在标准状态下放置6h以上,测量收缩率板的距离。制件背面有很多筋位,连续贯穿产品的长度和宽度方向,筋位冷却很快,在模具型芯里快速固化,冷却定型,限制了产品的收缩,产品尺寸偏长。成型周期对产品尺寸的影响主要是两方面
1.模具公模起到的是定型作用,周期越长,产品在模具中定型时间越长,尺寸越大。
2.成型周期与模温影响产品离开模具时候的温度,产品离开模具的温度越高,产品的后收缩越大,产品变形趋势越大。成型工艺对产品尺寸影响的因素有: 1.压力 大部分情况下决定产品的重量。 2.多浇口顺序阀的产品不同浇口的开启和持续的时间影响产品的尺寸,特别是对熔体流动方向比较单一的产品,如裙边等。 3.模具温度 模具温度高,相同冷却时间情况下产品出模温度高,后收缩大,产品会缩短。 尺寸不匹配的原因-成型工艺
-缩 痕
Sink Mark
定义:制件表面的下陷现象注塑过程中,塑料熔体以喷泉形式流动,表层的熔体因接触较冷的模壁形成固化层,而芯层处于熔融状态。充模结束后,表层已经冷却固化,而芯层才开始冷却,如果此时没有得到足够的保压补偿,芯层的冷却收缩拉扯表层,导致表层下凹形成缩痕;如果表层硬度足够抵抗收缩应力,则在制件中间形成缩孔,即真空泡 。缩痕:也叫缩水、凹痕、塌坑、瘪形等,是指制件在壁厚处出现表面下凹的现象,常在加强筋、沉孔或内部格网处出现。收缩不成,则形成空洞。料花 Silver Mark
定义:也叫银丝,制件表面出现的散射状外观缺陷塑料在充模过程中受到气体的干扰常常在制品表面出现银丝斑纹或微小气泡或制品厚壁内形成气泡时产生 ,这些气体的来源主要是原料中含有水分或易挥发物质或润滑剂过量,也可能是料温过高塑料受热时间长发生降解而产生降解气。飞 边
Flash
定义:塑料熔体冲出型腔的现象溢料:又称飞边、溢边、披锋等,大多发生在模具的分合位置上,有时在顶杆和镶块等位置也有。
以上就是100唯尔(100vr.com)小编为您介绍的关于模具的知识技巧了,学习以上的汽车注塑产品基础知识及问题分析思路知识,对于模具的帮助都是非常大的,这也是新手学习模具专业所需要注意的地方。如果使用100唯尔还有什么问题可以点击右侧人工服务,我们会有专业的人士来为您解答。
本站在转载文章时均注明来源出处,转载目的在于传递更多信息,未用于商业用途。如因本站的文章、图片等在内容、版权或其它方面存在问题或异议,请与本站联系(电话:0592-5551325,邮箱:help@onesoft.com.cn),本站将作妥善处理。
模具课程推荐
模具专业热门资料
模具专业技术文档
推荐阅读
