当前位置:首页 > 文章资讯 > 模具专业 > 压铸模具设计:压铸件的成功一步 浇口位置必须找准
压铸模具设计:压铸件的成功一步 浇口位置必须找准
一副压铸模具的顺利投产是一个压铸件成功开发的关键环节,而浇道系统的良好设计是保证压铸模具正常生产的前提。特别是一些有特殊要求(如气密性、表面粗糙度等)的产品,批量生产时,这些特殊要求往往成了考核一个压铸模具成功与否的关键指标。我们在实际生产中发现,虽然影响压铸件特殊要求质量的因素较多,但浇口位置的设置往往是一个不可忽视的环节,不恰当的浇口位置设置会造成一副模具的整体报废,或者模具生命周期大打折扣。本文以生产实践中压铸模浇口位置的设置对压铸件质量的影响做一简要的阐述。
压铸件浇道系统的设计需要通过对铸件的结构分析,并确定各种要求以后进行。设计浇注系统的一般过程是:
(1)选择浇口的位置。
(2)考虑引导金属流的流向。
(3)划分浇口的股数。
(4)设置浇道的形状和尺寸。
(5)确定内浇道的截面积。
在实际设计中,除浇口位置的选择是首先考虑的一步外,上述顺序只是一个大概考虑的步骤,先后次序并不是十分严格。其实,上述这几方面是互相影响、互相制约的。在考虑后一个步骤时,很可能要对前一个步骤已作的设计进行改变和调整。因此,必须根据具体情况全面地加以综合考虑,从而设计出符合要求的浇注系统。由于浇道系统的设计对压铸件质量影响的因素较多,本文仅就涉及浇口位置的选择对压铸件质量的影响进行讨论。
一、 浇口位置的选择原则
在模具设计时,浇口位置的选择,往往受到合金种类、铸件结构和形状、壁厚变化、收缩变形、机型类别(卧式、立式),以及铸件的使用要求等方面的限制,因此对压铸件来说,理想的浇口位置是很少的。在这些需要考虑的因素中,只能以满足最主要的需求来确定浇口位置,特别是一些特殊的需要。浇口位置首先受到压铸件外形所限定,同时还要考虑其他一些因素。一般来讲需要注意以下几个方面的问题。
(1)浇口位置应取在金属液填充流程最短、流至型腔各部位的距离尽量相近的部位,使填充路径减少曲折和避免过多的迂回。建议尽量采用中心浇口。
(2)浇口位置放在压铸件壁厚最厚的部位有利于最终压力的传递。同时,浇口开设在厚壁部位,对内浇道厚度的增加也留有余地。
(3)浇口位置应使型腔温度场的分布符合工艺要求,尽量满足金属液流至最远端的填充条件。
(4)浇口位置取在金属液流进入型腔不起旋涡且排气顺畅的部位,有利于型腔内气体的排除。生产实践中,要排除出全部气体是十分困难的,但针对铸件形状设法尽量多地排除气体则是设计时应考虑的问题。排气问题对有气密性要求的铸件应特别引起重视。
(5)对于框形铸件,浇口位置可以放在铸件投影范围内(见图1),若单个浇口填充良好,没必要采用多股浇口。
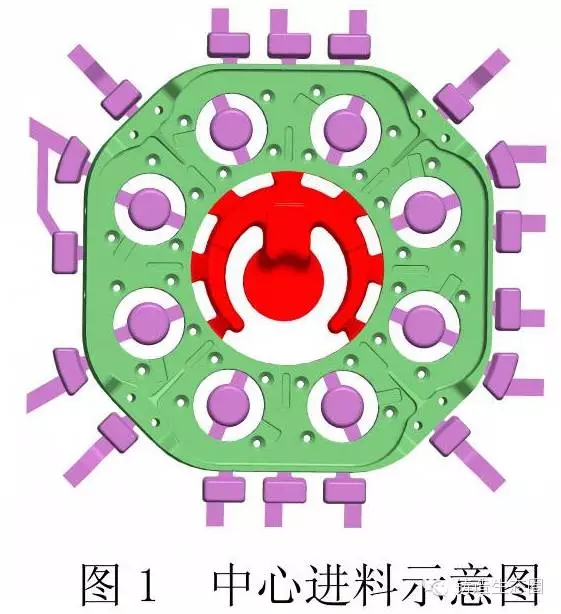
(6)浇口位置尽可能取在金属液流不正面冲击型芯的部位,应避免使金属流撞击型芯(或型壁)。因为撞击型芯后,金属液动能耗散剧烈,同时也易形成分散液滴与空气相混,使铸件缺陷增多。型芯被冲蚀后,产生粘模,严重时,被冲蚀的部位形成凹陷,影响铸件脱模。
(7)浇口位置应设置在铸件成形后容易去除或冲切浇口的部位。
(8)对有气密性要求或不允有气孔存在的压铸件,内浇道应设置在金属液最终都能保持压力的部位。
二、浇口位置影响压铸件质量的实例
2.汽车空调压缩机下壳体
如图2所示,是一款汽车空调压缩机的下壳体,该产品采用ADC12 合金,在DCC400压铸机上生产,冲头直径70mm,产品净重1040 g,渣包重量267 g,模具温度180~220℃,铝液温度650~680℃。
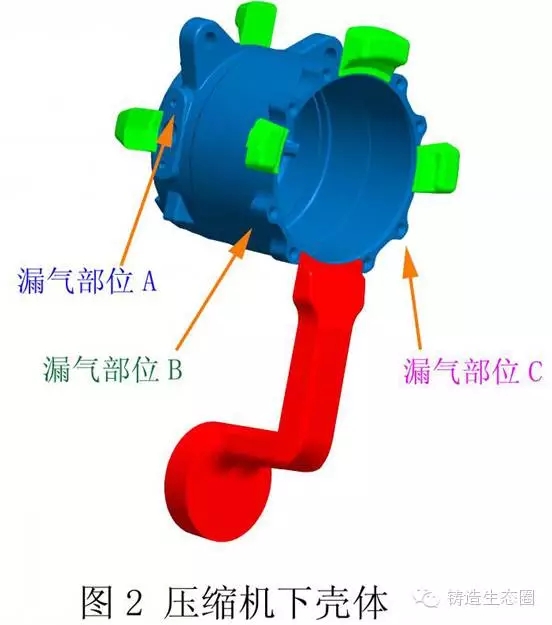
经过几次小批量生产发现,在图2所示的三个部位会出现数量不等的漏气现象,综合漏气比例甚至高达20%~30%。虽然一些渗漏的产品件后续经过浸渗处理能达到客户的检验标准,但是每次的浸渗费用较高,导致生产成本大幅上升,模具无法投入正常的生产。
为改善这一状况,我们对几次试制的压铸工艺进行了认真的计算分析,对该模具来说,原有的压铸工艺参数基本上都调整到了最佳的状态,是否是由于模具浇排系统的原因造成的这一问题呢?随即,我们便采用目前流行的压铸模拟流动分析软件对该模具的填充过程做模流分析,如图3所示。

从模流填充图上,我们可以看出,由于浇口开在产品件的端面上,在金属液填充时,图2所示的漏气部位B和C两处,恰好是金属液填充最末端所在的部位,由于这个产品的底部较厚,圆周的桶壁厚度较薄,金属液填充的末端在最后的增压阶段无法得到有效的补缩,内部存在组织疏松,最终造成铸件在此处漏气,气密性不合格。
由上述分析可知,该模具的浇口位置设置欠妥,导致了铸件气密性检测不合格,通过调整工艺参数仅能够对漏气的比例起到小幅改善,不能从根本上解决铸件漏气的问题。为彻底解决下壳体的漏气问题,我们决定对该模具的浇口位置进行更改,更改浇道位置后的铸件三维毛坯如图4所示。
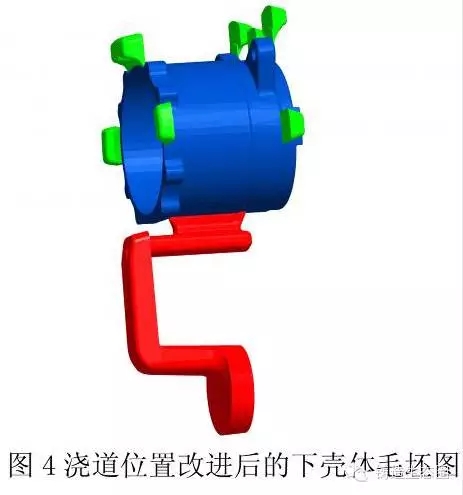
同时,我们对新的设计方案做了模拟填充分析,结果如图5所示。
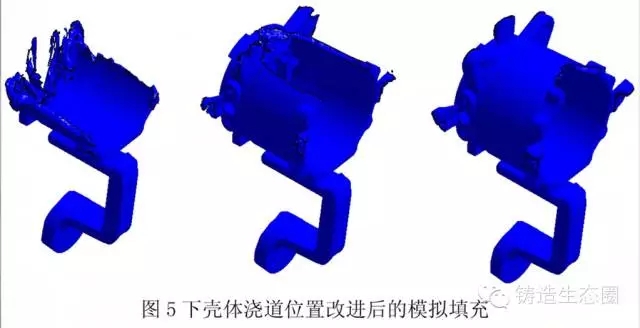
从更改浇口位置后所作的模拟分析可以看出,在新的填充方案中,金属液基本上是顺序填充,流动平稳,同时,在金属液流动的最末端还设计有一个较大的集渣包及一定面积的排气槽;从模拟结果上来看,更改后的方案要明显优于原有的设计方案。
随后,我们根据新的设计方案,对模具的浇口位置进行更改,经过小批试模,产品件的综合漏气率下降到了3.3%左右,达到了预期的更改效果。
2. 汽车机油泵壳体气密性的改善
图6所示的铸件是汽车上使用的一种机油泵的壳体,图示区域有气密性的要求,该产品是一个比较成熟的产品,已多次开过模具,在历次的模具使用过程中都存在产品气密性不良的问题,为改进原有模具存在的这个难题,我们决定从更改压铸模具的浇口位置入手,重新设计该产品的浇道系统。
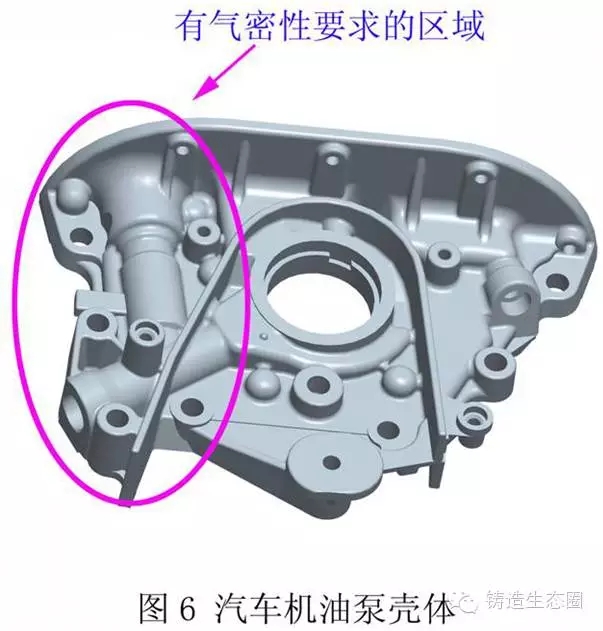
(1)根据浇口位置的选择原则可知,中心浇口的使用,可以使金属液的流程最短,同时有利于型腔内气体的排出,有利于铸件的气密性的提高。由于该产品的中间部位恰好有一个直径约40mm的通孔,完全可以采用中心进料的方式开模。对采用中心浇口的方案,我们作了模拟填充分析,图7为中心进料填充的机油泵壳体模拟
从图7可以看出,采用中心浇口后,恰恰是有气密性要求的区域发生了填充不良,大面积的气体被包裹进去,此方案对提高铸件的质量及气密性没有大的改善,有可能还会带来不良的后果,因此这个方案最终被否定了。经过大家的讨论研究,我们重新制定了第二套浇口位置的方案。
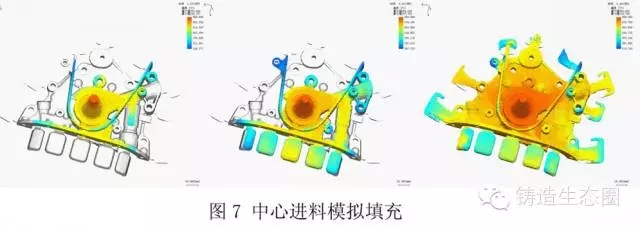
(2)根据压铸件的使用要求,采用多股分支浇道,将两个分支开设在有气密性要求的部位,加强对这一区域的填充和补缩。根据设计方案,新的浇道模拟结果如图8所示。
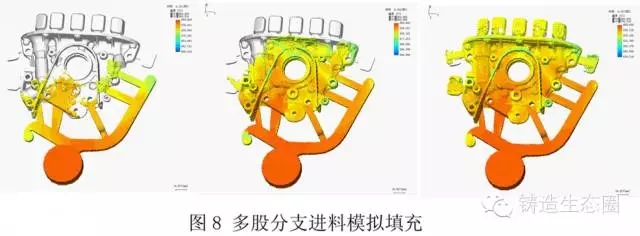
由图8可以看出,金属液进入型腔后对有气密性要求的区域的填充,是平稳推进的,没有喷射、卷气等现象发生,且浇口开设在有气密性要求的区域,在填充完毕后,能够很好地完成对该区域的增压补缩作用,可大大提高铸件此区域的的致密度,有效地减少气孔、缩孔的发生,对提高铸件的气密性非常的有益。
新开模具时参照第二套设计方案,重新开设了浇道位置和内浇道参数,经过试模和批量生产,该产品的气密性得到了很大的改善,漏气率下降到5%以内。
结语
通过上述分析,我们可以看到,一副模具浇道位置的设计存在许多不同的设计方案,如何从诸多的设计方案中遴选出最佳的设计方案,是设计精良的压铸模具必然要经历的一个过程,随着现代软件技术的发展,依靠先进的压铸模拟软件,可以帮助设计人员对浇道位置做出更好的选择,从而能避免模具使用后才发现的问题,再进行模具更改的尴尬,同时也能为企业节约一笔可观的模具更改费用。
来源:《金属加工(热加工)》转载请注明出处
以上就是100唯尔(100vr.com)小编为您介绍的关于金属加工的知识技巧了,学习以上的压铸模具设计:压铸件的成功一步 浇口位置必须找准知识,对于金属加工的帮助都是非常大的,这也是新手学习模具专业所需要注意的地方。如果使用100唯尔还有什么问题可以点击右侧人工服务,我们会有专业的人士来为您解答。
本站在转载文章时均注明来源出处,转载目的在于传递更多信息,未用于商业用途。如因本站的文章、图片等在内容、版权或其它方面存在问题或异议,请与本站联系(电话:0592-5551325,邮箱:help@onesoft.com.cn),本站将作妥善处理。
上一篇: 天哪,原来这些压铸缺陷都与模温有关?
金属加工课程推荐
模具专业热门资料
模具专业技术文档
推荐阅读
