新闻资讯
汽车发动机排气门导管的偏磨失效分析
摘要:对汽车发动机出现的排气门导管偏磨失效进行分析。对失效导管与正常导管的化学成分、组织结构、硬度和密度进行分析。结果表明,失效导管的碳含量过低,导致珠光体相对含量较少,进而造成导管的硬度过低,未能满足技术要求,是导致此次偏磨失效的主要原因。针对此导管的失效原因提出了相关改善措施。
关键词:排气门导管; 偏磨; 碳含量; 失效分析
气门导管与汽缸盖压配在一起,是控制气门正确开闭的重要装置,对气门起导向作用,使气门与气门座圈能正确贴合,保证气门作直线往复运动,同时气门杆上的热量能通过气门导管迅速传递给汽缸盖。气门导管的工作温度较高,润滑条件较差,其底部受燃气和高压空气作用。气门导管作为气门组的重要组成部分,如出现缺陷,将直接影响到整个发动机的工作状态和寿命,若严重磨损使得气门与气门导管的配合间隙增大,导致气门工作时在气门导管内晃动,进而造成气门头部和气门座圈偏磨,气门关闭不严等故障的产生。鉴于此,本文针对汽车发动机在正常工作过程中出现的气门导管严重偏磨失效,通过对此失效粉末冶金气门导管和合格气门导管的成分、组织结构、力学性能等进行检测和对比,分析了此气门导管严重偏磨失效的原因,并结合失效原因和此导管的生产工艺提出了相关的改善措施。
1 试验方法及步骤
观察偏磨失效导管宏观磨损形貌。利用洛氏硬度计测试导管宏观硬度,所得硬度为同一圆周10 个测量值的平均值。用排水法测试导管的密度。采用LEO-1450 型电子能谱对导管进行能谱分析,确定其化学成分。利用D/max-rB 型旋转阳极X 射线衍射仪检测导管的物相结构, 然后对导管进行金相组织观察。
2 试验结果
2.1 宏观形貌和磨损量
失效导管见图1,。
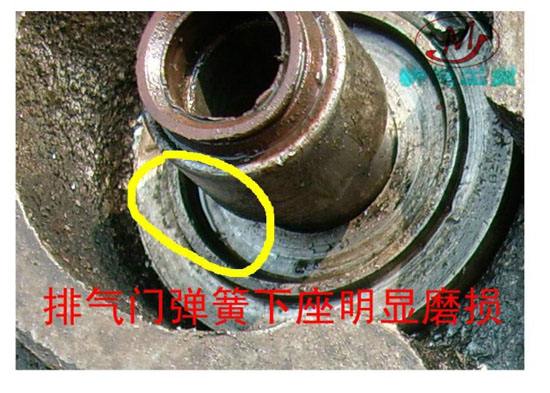
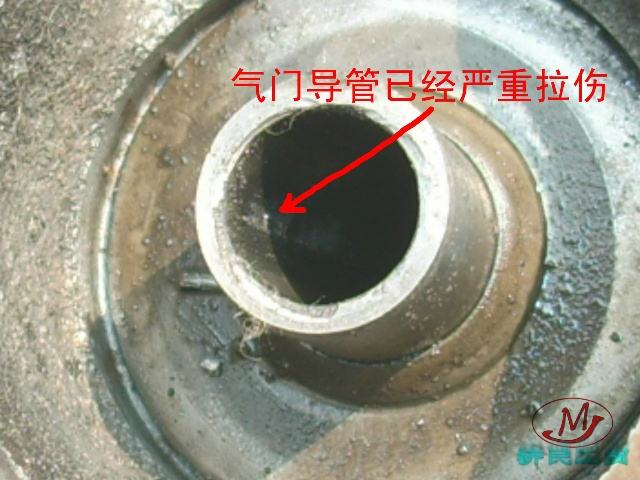
通过图1 可发现,左侧失效导管磨损严重,导管内孔呈椭圆形,且左侧壁厚较小,其失效形式为偏磨失效。测量整支失效导管两端的尺寸,失效导管的径向尺寸和磨损量见表1。其中,Ⅰ端为燃烧室端(与燃烧室接触),Ⅱ端为曲轮轴端(与曲轮轴接触)。
由表1 可看出,失效导管燃烧室端和曲轮轴端的最薄处磨损量分别为1.64、0.82 mm, 且磨损不均匀,从总体上看磨损程度严重,但磨损主要出现在一侧。
图2 为失效导管内孔表面的磨损形貌。该样品是从失效导管磨损最为严重的一端, 即燃烧室端所截取的一段,然后沿轴向切开,以便于观察失效导管内孔表面的磨损情况。
由图2 可看出,该失效气门导管端部表面存在少量燃烧附着物和机油,磨损严重且不均匀,磨损主要集中在一侧。导管内孔表面磨损带不均匀,在管壁较薄侧存在较多细条状、不连续、不均匀的沟纹,而管壁较厚侧的磨损表面较为光亮、沟纹较少。
气门在气门导管内处于倾斜状态, 而气门的倾斜使得气门导管两端受到侧向力的作用, 气门导管和气门杆不断相对运动造成受力侧的磨损不断增大,最终形成偏磨失效。从宏观磨损形貌观测结果可看出,磨损表面形成细长条状、不连续、不均匀的犁沟痕迹,属于磨料磨损。此失效导管为粉末冶金气门导管, 导管孔隙周围组织受往复冲击而脱落所产生的磨屑与燃气中夹杂的细微颗粒共同组成了存在于摩擦界面的磨粒颗粒。
2.2 化学成分
失效导管和正常导管的化学成分如表2 所示。可看出,失效导管与正常导管均为Fe-Cu-C 合金。正常导管和失效导管铜含量分别为1.01%和0.98%,符合这类气门导管的技术要求, 正常导管的碳含量为0.72%,符合技术要求,但失效导管的碳含量为0.57%,较正常导管低0.15%,且低于技术要求允许范围,此失效导管的化学成分未能达到成分设计的要求。
2.3 硬度与密度
失效导管与正常导管整体的表观硬度、密度对比如表3 所示。所测导管在同一圆周测得的硬度相差较小。可看出,失效导管和正常导管的密度相差很小,且均符合技术要求,但失效导管各部分硬度均比正常导管低14~17HRB,未达到技术要求。此失效导管的磨损类型为磨料磨损,磨料磨损主要决定于材料硬度和磨料中磨粒硬度的比值。此失效导管的硬度偏低,是导致严重磨损失效的主要原因。
2.4 X 衍射物相结构分析
失效导管和合格导管的X 射线衍射图谱如图3所示。其中图3(a)为失效导管衍射图谱,图3(b)为正常导管衍射图谱。由图3 可知,失效导管和正常导管的物相均为F(铁素体)、Fe3C(渗碳体)和游离Cu 等。
2.5 显微组织
在失效导管的严重失效端(燃烧室端)和正常导管所对应的一端分别截取金相试样,磨制径向检查面,用1%硝酸酒精进行腐蚀,得出失效气门导管和正常气门导管的显微组织(如图4 所示)。其中图4(a)、(c)为导管试样抛光后未经腐蚀的组织,其余为试样腐蚀后的组织;图4(a)和(b)为失效导管试样的组织,其余为正常导管试样的组织。由图4(a)、(c)可看出,失效导管和正常导管组织中均存在部分显微孔隙。
由图4(b)、(d)可看出,失效气门导管的金相组织为大量珠光体(黑白片层状),部分铁素体(亮白色块状)。而正常气门导管的金相组织为大量珠光体(黑白片层状)、少量铁素体(亮白色块状)和沿晶界分布的极少量渗碳体(带状)。通过对比可发现, 失效导管与正常导管的孔隙率基本相当, 但失效导管金相组织中铁素体相对含量明显高于正常导管,约占总体的30%。
由于失效导管和正常导管的密度和孔隙率基本相当图3 失效导管和正常导管的XRD 图, 因而排除了孔隙率过高导致材料硬度过低的情况。该失效导管和正常导管均为Fe-Cu-C 粉末冶金材料, 失效导管和正常导管铜含量分别为0.98%和1.01%,碳含量分别为0.57%和0.72%。在显微组织中很难直接观测到铜,可能是由铜含量较少所造成的,但结合相关研究成果与X 射线衍射分析可知,铜以游离态存在于晶粒表面。铜的添加能促进珠光体的共析转变,增加珠光体的相对数量,显著提高合金的硬度和强度,当铜含量低于3%时,合金硬度和强度随碳含量变化规律类似于Fe-C 合金。铁素体的晶格畸变程度和珠光体含量均能显著影响合金的硬度和强度。碳含量的增加使得铁素体的晶格畸变程度显著增加,同时,随碳含量增加,析出的Fe3C 逐渐增多,分布于铁素体上与铁素体形成两相组织,即珠光体,金相组织中铁素体数量逐渐减少,珠光体数量逐渐增加,该合金的硬度和强度迅速增加。由于铁素体为软韧相,耐磨性较差,而珠光体耐磨性较好,珠光体相对含量提高,合金的耐磨性也得到提高。在正常导管的金相组织中能发现少量的渗碳体,其能显著提高材料的硬度和强度,提高材料的耐磨性,而失效导管的金相组织中的渗碳体量很少,几乎观察不到。失效导管的碳含量明显低于正常导管,导致铁素体的晶格畸变程度较正常导管小,珠光体和渗碳体的相对含量较少,由于两者的共同作用,导致失效导管的各部分硬度和耐磨性低于正常导管。
3 改善措施讨论
3.1 影响碳含量的因素
以碳作为铁基粉末冶金合金添加元素, 其最大的困难是难以精确控制碳含量。原料粉末碳含量过低、粉末搬运过程中的扬起和产品生产过程中的脱碳均可能造成产品的碳含量低于技术要求。此导管采用推杆式连续烧结炉进行烧结, 保护气氛采用氨分解气氛。一般情况下,颗粒表面含少量以氧化物形式存在的氧,在高温下,颗粒表面的氧化物可能与碳发生反应导致脱碳。其反应式为:
为提高颗粒润滑性而加入的少量硬脂酸锌在烧结过程中会分解产生氧化物和水,均可能在一定程度上导致产品脱碳,同时,在进料和出料过程中会混入空气,空气中的氧气和水蒸气在接触导管后也可能导致脱碳。
3.2 改善措施
(1) 严格控制粉末原料质量。对粉末原料的化学成分进行检测, 确保粉末原料的化学成分满足成分设计的要求。
(2) 尽量减少粉末的储存时间, 减少颗粒表面的氧化现象,在搬运过程中尽量避免颗粒的扬起。
(3) 在生产过程特别是烧结过程中,露点温度、保护气氛流量等工艺参数的微小变动对气门导管含碳量有强烈的影响。适当降低露点温度,减少水蒸气在导管表面凝结的机会,同时加大保护气氛的流量,迅速带走气氛中混入的氧气和水蒸气,以减少脱碳现象的产生。
(4) 完善质量控制管理体系, 加强对产品质量的检测,对每批产品进行抽样,检测其化学成分、力学性能和组织结构等是否符合技术要求, 及时发现问题,以提高产品质量的稳定性。
4 结语
(1) 失效导管的碳含量低于技术要求允许范围,导致珠光体和渗碳体相对含量较少,进而造成导管的硬度过低,未能达到技术要求,是导致此次严重磨损失效的主要原因。
(2) 原料粉末碳含量过低、粉末搬运过程中的扬起和露点温度、保护气氛流量等产品生产工艺参数均可能导致产品的碳含量低于技术要求。
(3) 对粉末原料的化学成分进行检测, 确保粉末原料合格; 减少粉末的储存时间和搬运过程中的扬起;在烧结时控制合适的露点温度,同时加大保护气氛的流量,以减少脱碳现象的产生;完善质量控制管理体系,加强对产品质量的检测,提高产品质量的稳定性。
文章来源:AI汽车制造业
来源:期刊—热加工工艺
作者:张孝超1, 宣天鹏1, 戴泽玉2, 袁春2
( 1. 合肥工业大学材料科学与工程学院;2. 安徽金亿合金新材料有限公司)