新闻资讯
注塑机注射成型,模具在注塑机内是怎么工作的,大家看看
注射成型原理及其工艺过程 注射成型原理,
注塑机的工作原理与打针用的注射器相似,它是借助螺杆的推力,将已塑化好的熔融状 态(即黏流态)的塑料注射入闭合好的模腔内,经固化定型后取得制品的工艺过程,其原 理见图31-5。
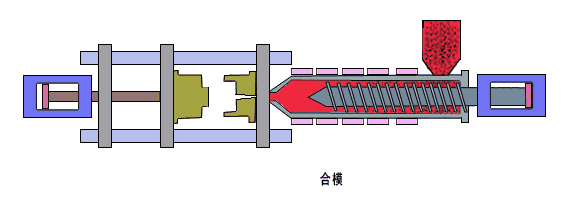
注射成型流程见图31-6。注射成型是利用塑料的热物理性质,把物料从料斗加人炮筒 中,炮筒外由加热圈加热,使物料熔融,在料筒内装有在外动力电机作用下驱动旋转的螺 杆,物料在螺杆的作用下,沿着螺槽向前输送并压实。物料在外加热和螺杆剪切的双重作用 下逐渐地塑化、熔融和均化。当螺杆旋转时,物料在螺槽摩擦力及剪切力的作用下,把已 熔融的物料推到螺杆的头部。与此同时,螺杆在物料的反作用下后退,使螺杆头部形成 -储料空间,完成塑化过程。然后,螺杆在注射油缸的活塞推力的作用下,以髙速、髙压, 将储料室内的熔融料通过喷嘴注射到模具的型腔中。型腔中的熔料经过保压、冷却、固 化定型后,模具在合模机构的作用下,开启模具,并通过顶出装置把定型好的制品从模 具中顶出落下。
注射成型工艺流程:
一、注射机类型:
结构:包括注射装置、合模装置、液压传动和电气控制系统。
二、分类:常见的三种分类方法如下:
卧式,立式,直角式。
通用型,专用型(独立性)。
螺杆式,柱塞式。
三、注射机的技术参数:
额定注射量、额定、最大;
额定注射压力;
额定锁模力;(超过额定锁模力的时候产品会产生毛边)
模具安装尺寸;(格林柱之间的尺寸)
开模行程等。(容模厚度与行程)
四、注射机的选用:
1、最大注射量的校核:塑件和水口料总重小于额定注射量的80%。
2、最大锁模力的校核:胀型力小于额定锁模力的80%。
胀型力=制品投影面积A×模具内压P
模具内压P通常取20—40MPa。
流动性好的塑料取20左右,
流动性中等的塑料取30左右,
流动性差的塑料取40左右.
五、注射成型工艺过程
1.成型前的准备:清理料筒、脱模剂。
2.注射过程:加料-——塑化——注射——保压——冷却——脱模。
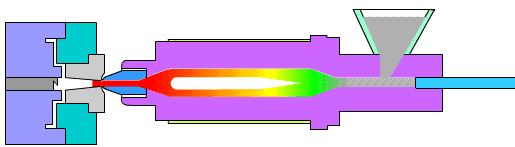
3.卧式注塑机的优缺点:
优点:掉料方便、装模方便、注射方便。
缺点:占地面积大。
六、塑件的后处理:
1.退火处理:目的是消除或减小内应力,提高制品表面韧性.
(1)烘箱或液体介质(如热水热油等);
(2)退火温度:塑件使用温度+(10~20)℃或塑件变形温度—(10~20)℃
2 调湿处理:主要针对尼龙制品,用于消除内应力,达到吸湿平衡,以稳定尺寸。
(2)热水温度:100—120 ℃。
七、注射成型工艺的三要素:
1.温度:主要指料筒温度和模具温度。
不同塑料的料温都不尽相同。
料温太低不利于塑化,料温太高,易导致塑件出飞边,严重时将导致塑料发生降解。
喷嘴的温度通常低于料筒的前段温度,以避免“流涎”现象。
2.压力:包括注射压力,塑化压力(即背压)、保压力和锁模压力。
塑件的尺寸越大,形状越复杂,壁厚越薄,要求注射压力越大。
流动性好的塑料及形状简单的塑件,注射压力较小;玻璃化温度及黏度都较大的塑料,应用较高的注射压力。
模具或熔胶温度较低时,宜用较大的注射压力。
对于同一副模具,注射压力越大,注射速度也越快。
3.时间:包括注塑时间、保压时间、冷却时间、顶出时间、开模时间、取产品时间、合模时间、喷脱模剂时间。
八、成型周期:
完成一次注射成型工艺过程所需的时间,包括合模时间,注射时间,保压时间,冷却时间,开模时间,顶出时间及其它时间(如放嵌件,喷脱模剂等)。其中保压时间和冷却时间占的比例最大,有时可达80%。
一文学会如何注射成型壁厚制件
塑料件的缩水问题(表面缩凹和内部缩孔),都是因为体积较厚的部位冷却时熔胶补充不足而造成的缺陷。我们常常会遇到无论如何加大压力,加大入水口,延长注射时间,缩水问题就是无法解决的情况。
在常用的原料当中,由于冷却速度快,PC料的缩孔问题可谓最难解决,PP料的缩凹和缩孔问题也是比较难处理的。
因此,当遇上厚大件比较严重的缩水问题时,就需要采取一些非常规的注塑技巧,不然就很难解决问题。
首先,在保证注塑件出模不变形的前提下,采取尽量缩短冷却时间的方法,让注塑件在高温下提早出模。此时注塑件外层的温度仍然很高,表皮没有过于硬化,因此内外的温差相对已不是很大,这样就有利于整体收缩,从而减少了注塑件内部的集中收缩。
由于注塑件总体的收缩量是不变的,所以整体收缩得越多,集中收缩量就越小,内部缩孔和表面缩凹程度因此得以减小。
缩凹问题的产生,是由于模具表面升温,冷却能力下降,刚刚凝固的注塑件表面仍然较软,未被完全消除的内部缩孔由于形成了真空,致使注塑件表面在大气压力的压迫下向内压缩,同时加上收缩力的作用,缩凹问题就这样产生了。而且表面硬化速度越慢越易产生缩凹,比如PP料,反之越易产生缩孔。
因此在将注塑件提早出模后,要对其作适当的冷却,使注塑件表面保持一定的硬度,令其不易产生缩凹。但若缩凹问题较为严重,适度冷却将无法消除,就要采取冻水激冷的方法,使注塑件表面迅速硬化才可能防止缩凹,但内部缩孔还会存在。象PP这样表层较软的材料,由於真空和收缩力的作用,注塑件还会有缩凹的可能,但缩凹的程度已大为减轻。
在采取上述措施的同时,若再采用延长射胶时间来代替冷却时间的方法,表面缩凹甚至内部缩孔的改善将会更好。
在解决缩孔问题时,因模温过低会加重缩孔程度,因此模具最好用机水冷却,不要使用冻水,必要时还将模温再升高一些,例如注塑PC料时将模温升到100度,缩孔的改善效果才会更好。但若是为了解决缩凹问题,模温就不能升高了,反而需要降低一些。
最后,有时以上方法未必能彻底将问题解决,但已经有了效大的改善,如果一定要将表面缩凹的问题彻底解决,适量加入防缩剂也是一个不得已的有较办法。当然,透明件就不能这样做了。
如果厚壁件表面还是存在缩痕,或者遇到偏壁等塑料件,那么引进气体辅助注塑成型将得到解决。
气体辅助注塑成型是通过把高压气体引入到制件的厚壁部位,在注塑件内部产生中空截面,完全充填过程、实现气体保压、消除制品缩痕的一项新颖的塑料成型技术。传统注塑工艺不能将厚壁和薄壁结合在一起成型,而且制件残余应力大,易翘曲变形,表面时有缩痕。
新发展的气辅技术通过把厚壁的内部掏空,成功地生产出厚壁、偏壁制品,而且制品外观表面性质优异,内应力低。轻质高强。
电视机、家电、汽车、家具、日常用品、办公用品、玩具等为塑料成型开辟了全新的应用领域,气辅注塑技术特别适用于管道状制品、厚壁、偏壁(不同厚度截面组成的制件)和大型扁平结构零件。
气体辅助装置 :包括氮气发生和增压系统,压力控制单元和进气元件。气辅工艺能完全与传统注塑工艺(注塑成型机)衔接。
减轻制品重量(省料)可高 40%,缩短成型周期(省时达30%,消除缩痕,提高成品率;降低注塑压力达60%,可用小吨位注塑机生产大制件,降低操作成本;模具寿命延长、制造成本降低,还可采用如粗根、厚筋、连接板等更稳固的结构,增加了模具设计自由度。