新闻资讯
冲压模具培训:常见五大类问题及其解决方案总结归纳
冲压是大批量零件成型生产实用工艺之一。在冲压生产过程中,模具出现的问题最多,它是整个冲压生产要素中最重要的因素。直接影响到生产效率和成本。影响到产品的交货周期。模具问题主要集中在模具损坏、产品质量缺陷和模具的刃磨方面,它们长期困扰着行业生产。只有正确处理这几个关键点。冲压生产才能够顺利进行。
冲床便是一台冲压式压力机。在普通生产中,冲压工艺由于比较传统机器加工来说有节约材料和成本,产量高,对操纵者技能要求不高及通过种种模具使用能够做出机器加工所无法到达的产品这些长处,因此它的用处越来越普遍。但随之而来的模具问题也会越来越多。模具故障是冲压生产中最容易出现的问题,常常造成停产,影响产品生产周期。因此,必须尽快找到模具故障原因,合理维修。
(1)凸模磨损太快
模具间隙偏小,通常模具总间隙为材料板厚的15%,25%。
凸凹模具的对中性不好,模座和模具导向组件及转塔镶套精度不够等情况形成模具出件不顺。
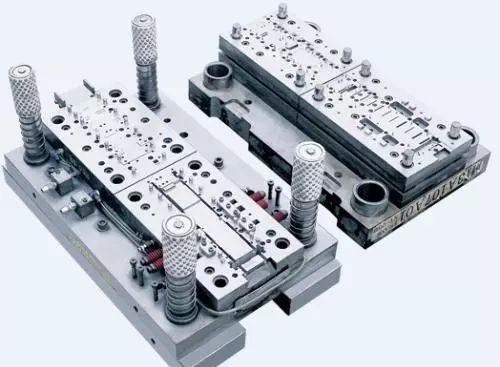
凸模温度过高,主要是由于长期不间断生产,使模具冲压形成冲头过热。
模具刃磨方法不对,形成模具退火,磨损加剧。
部分的单边冲切,如步冲、冲角或剪切时,铝合金门窗配件侧向力会使冲头倾向一边,该边的间隙减小,形成模具磨损严峻,假如机床模具安装精度不高,还可能会使冲头偏过上模,形成凸模和凹模破坏。
(2)模具带料问题
模具带料会形成废料反弹,其相干要素:
1、模具刃口的尖利程度,刃口的圆角越大,越容易形成废料回弹。
2、模具的入模量,机床每个上位的入模量是肯定的,模具大模量小,容易形成废料反弹。
3、模具的间隙需要合理,假如模具间隙不适宜,容易形成废料反弹。
4、被加工板材表是否存在较多的油物。
5、弹簧原件出现破坏。
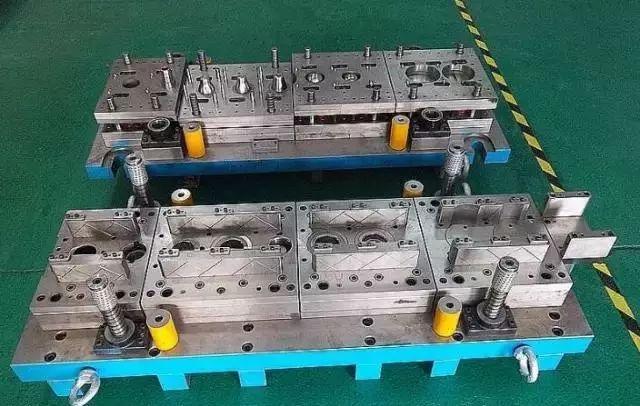
防止模具带料的办法:
1、运用专用的防带料凹模。铝合金门窗配件
2、模具经常刃磨保持尖利,并退磁处置。
3、增大凹模间隙。
4、接纳斜刃n模具替代平刃口模具。
5、模具安装退料器。
6、适当的增大模具的入模量。
7、检查模具弹簧或卸料套的磨损程度。
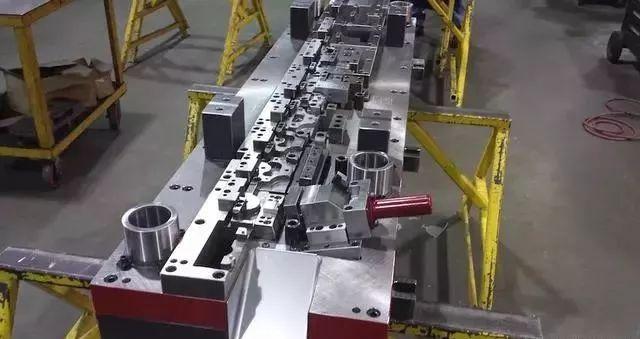
(3)模具对中性
模具在运用时容易发作冲芯各侧地位的磨损量差别,有的部分有较大划痕,磨损较快,这种状况在细窄的长方模具上特别显着。该问题主要缘由:
1、机床转塔设计或加工精度不够.主要是上下转盘间模具安装座的对中性不好。
2、模具的设计或加上精度不能满意要求。
3、模具凸模的导套精度不足。
4、模具间隙选择不适宜。
5、模具安装座或模具导套由于长期运用磨损形成对中性欠好。
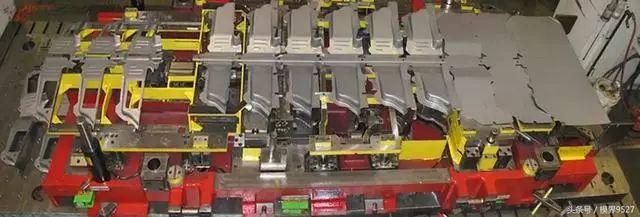
为防止模具磨损不同步应:
1、定期维护对中芯棒对机床转塔和安装座进行对中性检查调解。
2、实时更换模具导套并选用适宜间隙的凸凹模具。
3、使用全导程模具。
4、增强操作工的责任心,发现后实时查找缘由,避免形成更大事故。
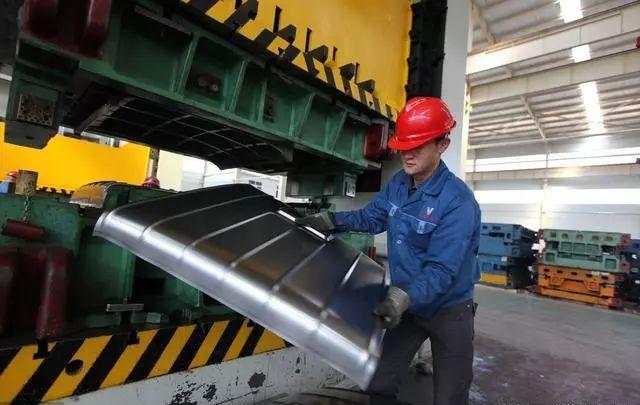
(4)特别成形模具运用
为满意生产需求,经常需求运用成形模具或特别模具,主要有桥形模具、百叶窗模具、沉孔形模具、翻孔攻螺纹模具、凸台模具、拉伸模具、组合式模具等,运用特别或成形模具町以大家进步生产产量,但足成形模具价钱较高,通俗是平凡模具的4-5倍。为避免失误,应留意和遵照以下规定:
1、模具安装时进行方向检查,确保模具凸凹模安装方向一致。
2、依据要求准确调解模具的冲压深度,每次调解最好不超越0.15mm。
3、运用较低的冲切速率。
4、板材要平整无变形或翘起。
5、成形加工俯置应尽量远离夹钳。
6、成形模具运用时应避免向下成形操纵:
7、冲压时按照先平凡模具冲压,最后运用成形模具。
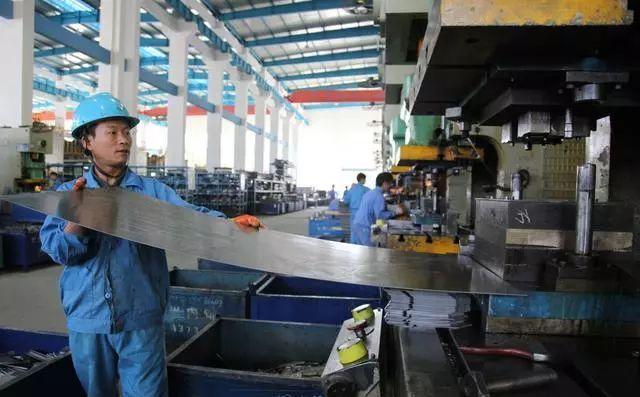
(5)模具弹簧疲劳
冲床模具运用中容易无视的一个问题,铝合金门窗配件就足模具弹簧的运用寿命,模具弹簧也需求定期进行保养或更换,但是国内很多用户对设备和模具能进行保养,却往往无视了模具弹簧的保养,乃至有的用户弹簧多年就没有更换过,同工位或模具经常出现破坏或冲压带料,却无法找到缘由,其后更换模具弹簧后,问题得到透彻处理。关于不同的冲床设备和模具,其模具弹簧也有所差别。假如保养不妥,容易发生模具带料并能够破坏模具或导套,形成不必要的损失。
(6)模具损坏
模具损坏是指模具开裂、折断、涨开等,处理模具损坏问题,必须从模具的设计、制造工艺和模具使用方面寻找原因。首先要审核模具的制造材料是否合适,相对应的热处埋工艺是否合理。通常,模具材料的热处理工艺对其影响很大。如果模具的淬火温度过高,淬火方法和时间不合理,以及回火次数和温度、肘间选择不当,都会导致模具进入冲压生产后损坏。落料孔尺寸或深度设计不够,容易使槽孔阻塞,造成落料板损坏。弹簧力设计太小或等高套不等高,会使弹簧断裂、落料板倾斜.造成重叠冲打,损坏零件。
冲头固定不当或螺丝强度不够,会导致冲头掉落或折断。
模具使用时,零件位置、方向等安装错误或螺栓紧固不好。工作高度调整过低、导柱润滑不足。送料设备有故障,压力机异常等,都会造成模具的损坏。如果出现异物进入模具、制件重叠、废料阻塞等情况未及时处理,继续加工生产,就很容易损坏模具的落料板、冲头、下模板和导柱。
(7) 卡模
冲压过程中,一旦模具合模不灵活,甚至卡死,就必须立即停止生产,找出卡模原因,排除故障。否则,将会扩大故障,导致模具损坏。
引起卡模的主要原因有:模具导向不良、倾斜。或模板间有异物,使模板无法平贴;模具强度设计不够或受力不均。造成模具变形,例如模座、模板的硬度、厚度设计太小,容易受外力撞击变形;模具位置安装不准,上下模的定位误差超差。或压力机的精度太差,使模具产生干涉;冲头的强度不够、大小冲头位置太近,使模具的侧向力不平衡。这时应提高冲头强度,增强卸料板的引导保护。
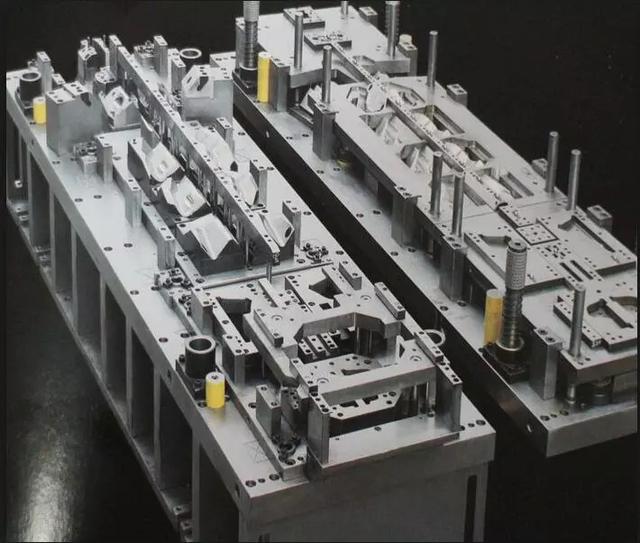
三、模具损坏和维修
冲压生产的模具费用高.通常模具费占制件总成本的1/5-1/4。这是因为,除模具制造难度大、成本高外。投入生产后的模具修理和刃磨维护费用也高,而模具的原始造价仅占整个模具费用的40%左右。因此,及时维修模具,防止模具损坏,可以大大降低冲压生产的模具费用。
一般来说,模具损坏后,还有一个维修和报废的选择问题。冲压模具的非自然磨损失效,例如非关键零件的破坏。以及小凸模折断、凸模镦粗变短、凹模板开裂、冲裁刃口崩裂等故障.大部分可以通过维修的方法使其完全恢复到正常状态,重新投入冲压生产。但是。当模具的关键件严重损坏,有时凸、凹模同时损坏。一次性修复费用超过冲模原造价的70%,或者模具寿命已近。则维修的意义不大,这时应该考虑报废模具:除大型模具、结构复杂的连续模外。当模具维修技术过于复杂、修模费用太大,难度大必然使维修周期过长,严重影响冲压的正常生产,应选择提前失效报废,重新制造模具。
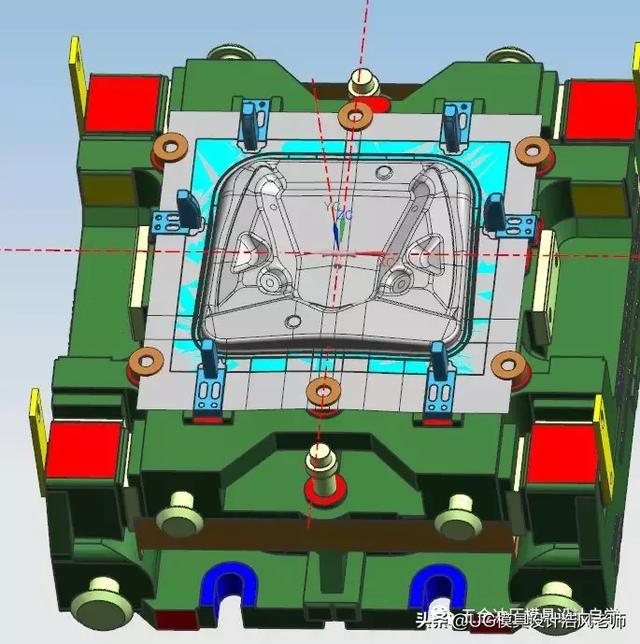
冲压生产效率和成本对模具的依赖性很大。对生产过程中模具出现的故障,应具体问题具体分析,制定正确的维修方案。及时解决模具损坏、卡模、刃磨和产品质量缺陷等问题。处理好模具维修与报废的关系,才能减少停产修模时间,缩短生产周期,保证冲压生产的正常进行。