新闻资讯
汽车冲压模具废料滑落问题解析
对冲模废料滑落问题,结合理论分析及现场实际状态进行深入研究,针对模具中部分典型位置,从前期工艺结构设计方面进行解析。提出实用的解决方案,在该理论指导下,使废料滑落不畅的问题在模具设计初期可以得到较好预防,减少后期调试整改周期,降低生产成本。
近年来国内汽车行业陆续采用冲压半自动化、全自动化生产。而半自动化、全自动化冲压生产中,冲压废料滑落问题往往是影响生产线体效率中较为突出的问题。因此,冲压废料处理得好坏直接影响着冲压连续生产的效率。但是,由于设计人员技能不足,现场生产经验缺失等因素,造成部分问题流入下工序,当模具进入调试期时,只能依靠经验丰富的调试人员根据实际情况进行调整,需多次进行在线整改,占用大量的设备资源、人力、周期。本文针对模具中部分典型位置,从现场实际问题入手,解析问题发生原因及解决对策。为后期设计提供参考。
某车型顶盖外板修边序二级切刀位置
原因分析
分析设计图纸及工艺方案,得出造成废料卡滞的原因主要有两个的结论,一是此位置二级切刀为平行布置且刃口朝向一致,当废料切断后由于切刀刀背位置使废料产生左右移动,碰触到另一侧切刀,限制了废料的旋转,导致无法下滑(图1)。二是二级切刀自身带有约15°斜角,但图纸中挡料杆设计在切刀刃口后侧,当废料切断后进一步限制了废料沿二级切刀刃口端面斜角下滑可能性(图2)。
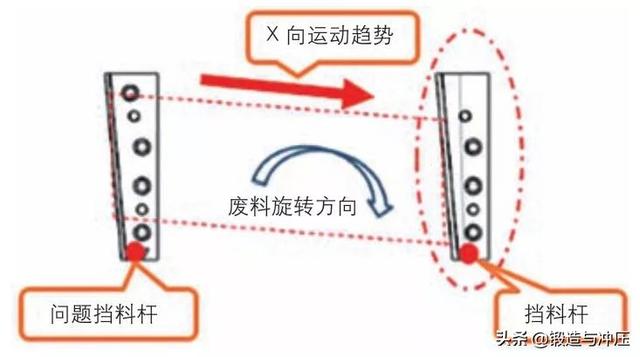
图1 废料卡滞运动模拟
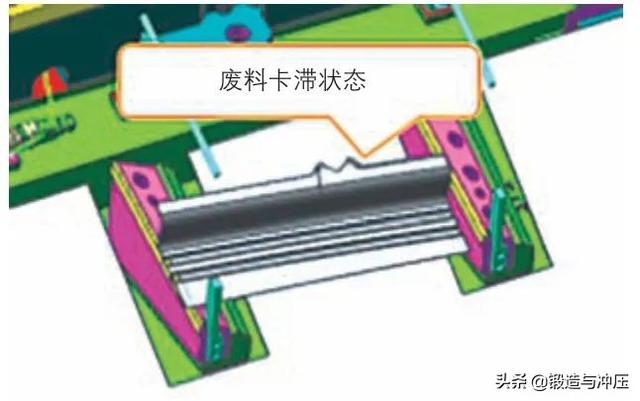
图2 卡料状态
解决对策
根据不同的废料长度,二级切刀布置通常为两种形式。形式一:两刀式切刀——二级切刀成10°开口状相对布置,切刀刃口后侧设计挡料杆。二级切刀刃口下部背空倒斜角处理,废料滑落趋势模拟及具体布置形式如图3 所示。形式二:三刀式切刀——两端的二级切刀成10°开口状相对布置,挡料杆设计在切刀刃口后侧(中间不设计挡料杆)。中间切刀角度竖直布置,切刀背空位置倒斜角,如图4 所示。
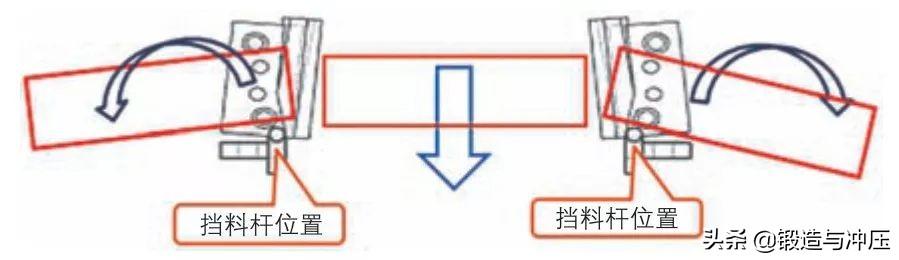
图3 两刀式切刀布置及废料滑落分析
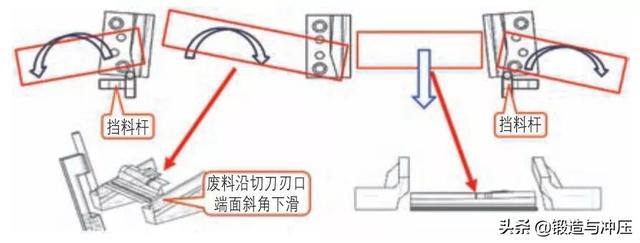
图4 三刀式切刀布置及废料滑落分析
在使用二次切刀时必须综合考虑废料二次切断时滑料的滑落空间,滑动轨迹以及废料二次切断时废料飞溅的方向,在设计初期对二次切刀实际生产时可能出现的各种问题进行分析预防。
某车型翼子板侧修位置
原因分析
分析卡料状况及工艺方案,造成废料卡滞的原因主要是由于废料刀刃口朝向导致废料滑道宽度小于废料长度,限制废料只能通过旋转滑出模具,但设计在废料滑出方向的斜楔驱动又对废料旋转造成阻碍,导致废料无法掉落(图5)。
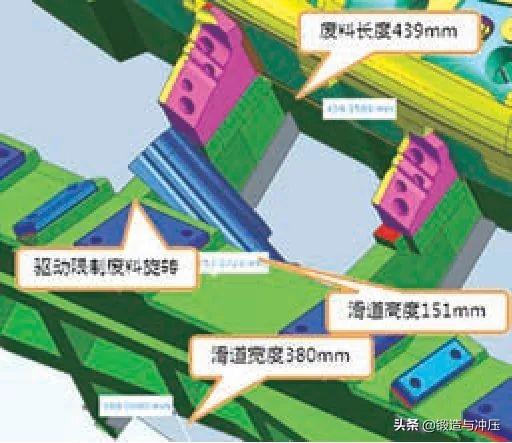
图5 斜楔位置废料卡滞模拟解析
解决对策
针对侧修位置废料滑出困难可以采用从以下工艺排布和结构设计两个方面单独或共同进行设计优化。
工艺排布方面优化:调整废料刀2 刃口方向,使之与废料刀3 形成相对布置,同时优化废料刀2 下模位置支撑筋截面形状,保证废料滑道宽度大于废料最大对角长度至少30mm。同时,降低滑料板高度,增加废料动能,使之可以更加顺利的滑出模具。对于制件边缘废料可以适当增加模具宽度或弹顶销的辅助装置,提升滑料效率。需要注意的是,在模具结构设计过程中,应注意此位置废料是否存在翻转的风险。(翻转轴可通过将拉延理论边界分别在两处废料切断位置最外侧两点连线进行简单确认)。同时,尽可能的避免设计过桥结构,如无法避免,也应保证过桥高度大于废料翻转高度。在角部位置设计废料排出气缸,防止废料被侧修刃口及两侧废料刀架起,如图6所示。

图6 优化后工艺形式及支撑筋布置
结构设计方面优化:上模滑车侧修镶块取消后侧挡墙,镶块下增加定位键,这样可将下模驱动位置整体抬高,同时,将驱动与滑车间的导板安装到滑车位置,这样下模驱动位置可以取消导板挡墙,增大滑料空间,如图7 所示。
在遇到同方向多废料刀切断的情况,如均为正修,应避免设计过桥结构。如侧修无法避免过桥,也应优先保证中间位置废料下滑,通过改变支撑筋位置,优化模具结构形式等措施,降低废料卡滞的风险。
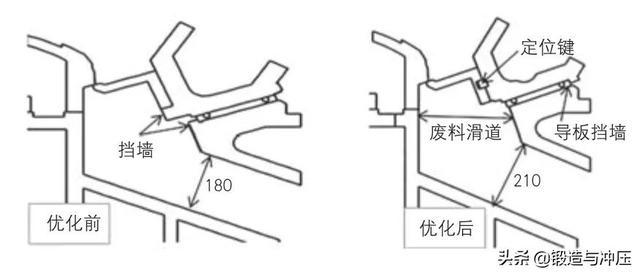
图7 斜楔位置优化前后对比
某车型车门内板制件中间位置
原因分析
当制件中间位置存在较大废料时,废料从制件脱离到跌落至滑板的过程中状态不稳定,出现翻转情况,当废料出现图8 中红色状态时,立起后的废料卡滞在模具与废料滑板之间。
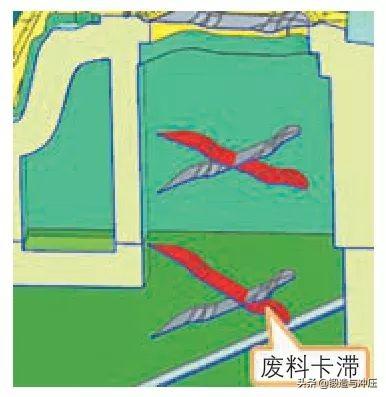
图8 制件中间位置废料卡滞状态
解决对策
针对制件中间位置冲大孔废料,同样可以从工艺排布和结构设计两个方面进行设计优化。
工艺排布方面优化:当中间位置废料需要分切时,避免出现废料尖角特别多情况,见图9,按此工艺排布后,在OP40 上废料周圈均为修边尖角,这样,当OP40 修边完成后无论废料从哪个方向滑出模具均存在修边尖角与铸件滑道侧壁挂住的情况,引起废料卡滞。所以在工艺排布初期应尽量避免废料尖角。保证废料形状越简单越好。
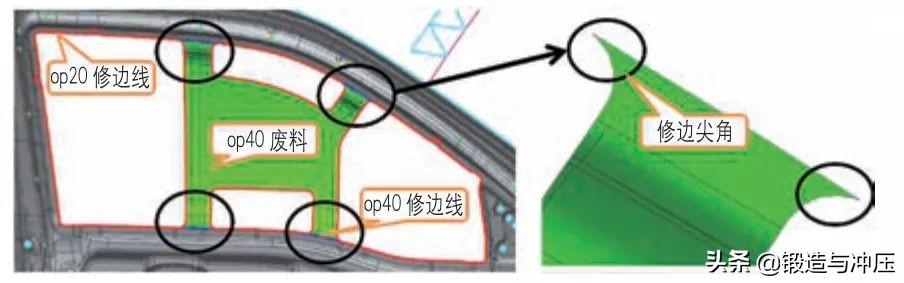
图9 废料尖角问题
结构设计方面优化:对于制件中间位置较大的废料,在模具结构设计时,在废料出料方向前侧上模镶块位置增加弹顶销,使废料一端向下倾斜,刃口下方预留出废料旋转的空间。同时在出料方向后侧的下模滑道位置设计支撑部件,确保废料在滑道内的状态,如图10 所示。
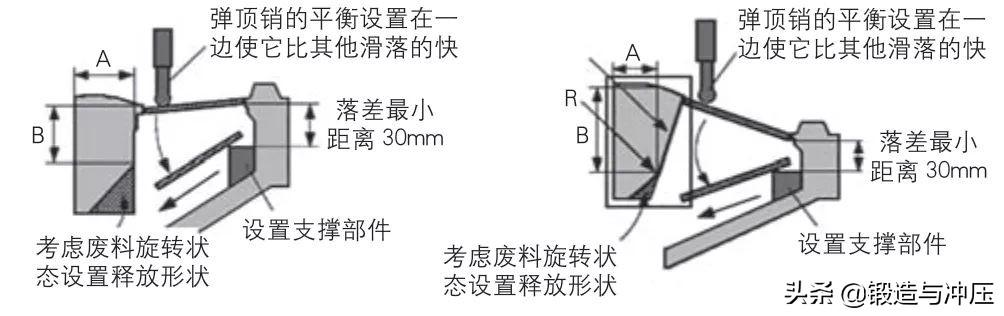
图10 制件中间位置结构优化方案
在自动化生产中,每批次制件数量较多,中间废料一旦出现卡滞,就会造成连锁效应,如果不能及时发现,模具就会存在损坏的风险。需要我们在结构设计时格外注意。
结束语
自动化生产过程中,真正影响生产效率的往往是废料下滑这类的问题,本文通过具体的案例结合自身设计经验,详细的介绍了三种常见废料滑出问题及其解决方案,从而将问题前置,尽可能的减少后期问题的发生,最大限度地减少装配调试的时间,缩短模具制造周期,提高企业的市场竞争力。
—— 来源:《锻造与冲压》2019年第18期