新闻资讯
注塑模具塑件翘曲(变形)怎么解决
注塑模具塑件翘曲(变形)怎么解决
翘曲指的是塑件的形状与图纸的要求不一致,如图3-33~图3-35所示,也称变形。翘曲通常是因塑件的不均匀收缩而引起的,但不包括脱模时造成的变形。
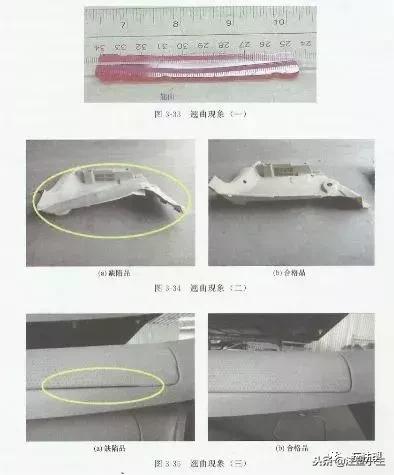
导致塑件成型后翘曲的原因及相应的解决方法有以下几点。
①分子取向不均衡,如图3-36所示。为了尽量减少由于分子取向差异产生的翘曲变形,应创造条件减少流动取向或减少取向应力,有效的方法是降低熔体温度和模具温度,在采用这一方法时,最好与塑件的热处理结合起来,否则,减小分子取向差异的效果往往是短暂的。热处理的方法是:塑件脱模后将其置于较高温度下保持一-定时间再缓冷至室温,即可大量消除塑件内的取向应力。
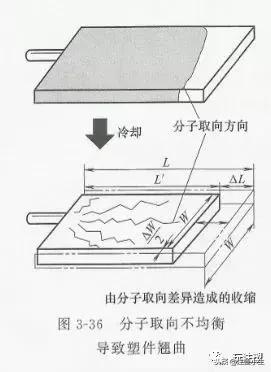
②冷却不当。塑件在成型过程中冷却不当极易产分子取向方向生变形现象, 如图3-37所示。设计塑件结构时,各部位的断面厚度应尽量-致。塑件在模具内必须保持足够的冷却定型时间。对于模具冷却系统的设计,应注意将冷却管道设置在温度容易升高、热量比较集中的部位,对于那些比较容易冷却的部位,应尽量进行缓冷,以使塑件各部分的冷却均衡。
③模具浇注系统设计不合理。在确定浇口位置时,不应使熔体直接冲击型芯,应使型芯两侧受力均匀;对于面积较大的矩形或扁平塑件,当采用分子取向及收缩大的塑料原料时,应采用薄膜式浇口或多点式浇口,尽量不要采用侧浇口;对于环形塑件,应采用盘形浇口或轮辐式浇口,尽量不要采用侧浇口或点浇口;对于壳形塑件,应采用直浇口,尽量不要采用侧浇口。
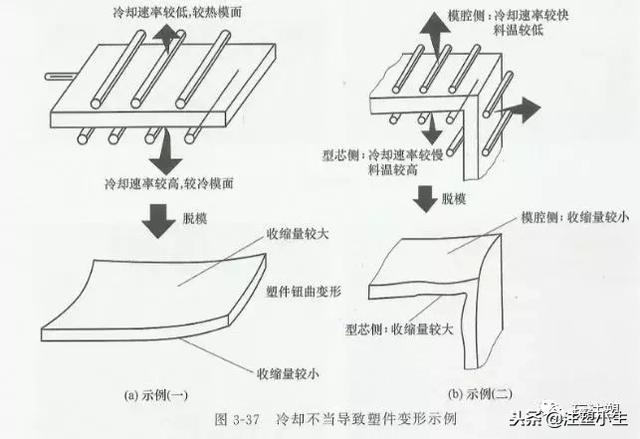
④模具脱模及排气系统设计不合理。在模具设计方面,应合理设计脱模斜度、顶杆位置和数量,提高模具的强度和定位精度;对于中小型模具,可根据翘曲规律来设计和制造反翘模具。在模具操作方面,应适当减慢顶出速度或顶出行程。
⑤工艺设置不当。具体的表现有:模具、机筒温度太高;注射压力太高或注射速度太快;保压时间太长或冷却时间太短。应针对具体情况,分别调整对应的工艺参数。
⑥塑件结构不合理,如:壁厚不均,变化突然或壁厚过小;制品结构造型不合理,没有加强结构来约束变形。