新闻资讯
吹塑成型工艺及模具设计要领
吹塑成型技术(Forming Technology Blow Molding)
吹塑成型技术通常用于大规模生产中空包装容器的生产,是一个迅速生产大量的薄壁零件的方法。
一.吹塑成型技术精简篇
吹塑成型技术分为三种不同方法:挤出吹塑(EBM),注射吹塑(IBM)和注射拉伸吹塑(ISBM)。每个流程都有其特定的工艺,适用于不同的行业。
❶ 挤出吹塑(EBM)
挤出吹塑EBM(Extrusion blow molding)
EBM在大多数应用实例中适用,且备受欢迎,因为其设备和运行成本较低。它算是一种万能的工艺,可用于生产各种形状的产品,材料的选择也很广泛。其容器可以做整体处理,并且实现多个分层效果。
挤出吹塑EBM
第一阶段生产的过程中,传统的挤压装配会将塑料聚合物加热后挤压到容器。聚合物被挤压装置挤压在芯棒中成为圆管状,称为挤压半成品,其挤压的过程是连续的。
第二阶段,一旦半成品已达到足够长度,两边模具会顺势关闭,圆管状的半成品被模具的底部边缘修剪密封,形成瓶底。随后,半成品顶部被型坯切刀裁剪,横向转移到第二个设备,那里的空气吹针会将气体吹入设备,把聚合物撑大,迫使半成品在模具内贴合内壁,形成需要的形状。随后热聚合物会因为接触到冰冷的模具内壁而凝固.
第三阶段,冷却,将模具内半成品充分冷却后打开模具,就可以得到需要的产品。取出之后,由工人将容器进行修整,就得到了最后的成品。
❷ 注射吹塑IBM(Injection blow molding)
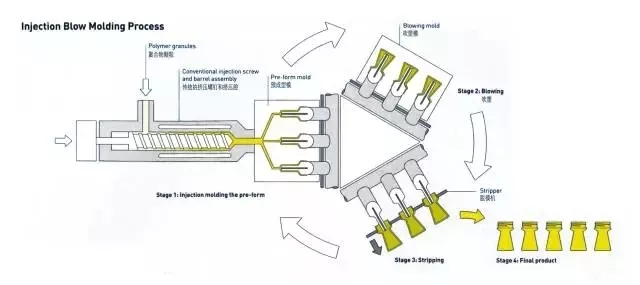
注射吹塑IBM是一种相对于挤出吹塑EBM更为精确的工艺,适用于要求更高的工业应用,如医疗和化妆品包装容器。可以用于生产产品尺寸要求非常准确的容器。
注射吹塑IBM的加工过程核心是基于一个旋转装置。
第一阶段,预成型加工模块将加热后的聚合物原料注入芯棒,完成顶端细节加工后,芯棒和预成型模块会旋转120°。
第二阶段,空气吹到预成型加工模块中,迫使半成品形成模具的形状。
第三阶段,充分冷却后,模块旋转120°,剥离芯棒,完成注塑。剥离之后,会进行修整,形成需要的产品。
❸ 注射拉伸吹塑ISBM(Injection Stretch Blow Molding)
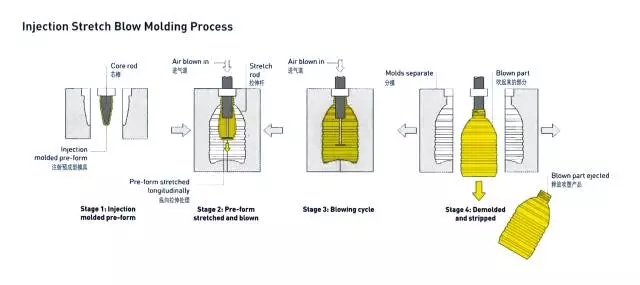
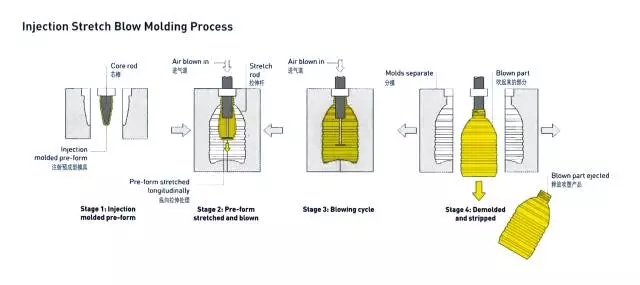
注射拉伸吹塑ISBM通常用于生产高质量的透明质感等,要求明确的容器,如PET材料的水杯。循环注入方法可以确保产品的精确度,循环拉伸方法可以提供优越的力学性能。ISBM尤其适用于饮料、农药和个人护理产品包装。
注塑吹塑成型过程中,注塑预成型是被送到型芯上,进入吹塑模腔中吹塑成型的。
制品的质量和壁厚取决于注塑模腔的形状。改变注塑参数仅仅对制品重量有很小的调节。
注塑模具使用的材料为钢。为了提高充模质量,经常对模具表面进行化学处理。
对于蘸料吹塑成型,吹塑杆侵人蘸料室。颈环被充满后,吹塑杆拉回“通过设计蘸料室活塞的动作可以改变型坯的轴向壁厚。然后型坯由吹塑模具移走,吹塑制品。在此之后,吹塑杆退回,吹塑过程用一个辅助吹塑杆继续进行。因为注塑吹塑成型和蘸塑吹塑成型不用切边,可以用铝制造它们的模具。
第一阶段,ISBM过程使用和IBM相同的技术,其中预成型过程形式是和注射成型一样,将聚合物注射到芯棒进行加工。
第二阶段,ISBM芯棒拉伸杆被移除和替换。预成型模块插入到吹制模,夹紧并关闭。
第三阶段,通过拉伸杆定位模具纵向,并向模具中吹入空气,将聚合物吹到模具边缘。
第四阶段,冷却后模具打开,从拉伸杆部分剥离,从而得到产品。
二.吹塑成型的工艺及影响吹塑加工成型的因素。
1、吹塑原料的选择
在吹塑中原料的选择很重要。首先要求原料的性能满足制品的使用要求,其次是原料的性能必须符合吹塑工艺的要求。高密度聚乙烯取0.94-0.96克/厘米熔体指数范围。低熔体指数树脂吹塑时有利于防止型坯下垂,容易得到壁厚均匀的管坯。但是螺杆转速增高时,低熔体指数的树脂外观粗糙。因此对于上述熔体指数范围的选用,大中型吹塑制品以防止型坯下垂为主,宜偏低一些;小型吹塑制品选偏高一些。
2、温度的控制
在挤出管坯过程中温度控制的精确度对于管坯质量影响很大。例如温度过低型坯表面粗糙,温度高表面光泽好,但下垂严重。在挤出聚氯乙烯等容易热降解的树脂时,还要注意控制温度使其不超过降解温度。
3、螺杆转速对挤出管坯的影响
螺杆转速是影响管坯质量的一个重要因素。高的挤出速度能够提高产量,减少型坯下垂,但是型坯表面质量下降。尤其是剪切速率增大造成某些塑料,如高密度聚乙烯,可能出现熔体破裂现象。而且转速提高时大量摩擦热的产生使聚氯乙烯等塑料有瞬间降解的危险。所以一股吹塑机都选用大一点的挤出装备,使螺杆转速在70转/分以下。
4、口模对挤出管坯的影响
口模是决定型坯尺寸及形状的重要装置,所以要求内表面光洁度应达到10且尺寸必须按设计要求加工。口模定型段尺寸一般可选用8倍口模芯棒之间隙数值。
可见,要做好吹塑产品,好的选料,吹塑工程师对于吹塑机器的温度控制,对螺杆和口模的选择是非常讲究的。
三.这些吹塑技术的区别
再来说说这些吹塑技术的区别,最大的区别就是每个技术之间容纳的能力不同。
IBM通常生产的容器空间为3毫升到1升(0.005 到1.760品脱),而ISBM可以生产50毫升和5升(0.088 到8.799品脱)的容器。EBM可以创建最大的容积,可以介于3毫升和220升(0.005到387品脱)。
各自的优点:EBM的主要优点是,在选材上可以有更多选择进行复杂的造型生产。而ISBM可以用来产生有更多细节的容器。ISBM在拉伸吹期间,可以大大增加调整产品的机械强度。
应用场景方面:EBM主要用于医疗、化工、消费品行业容器,如药片瓶和药水瓶瓶,快消品包装。IBM主要用于精确度更高的快消品包装和医疗包装。ISBM主要在个人护理产品包装,农用化学品包装,一般化学品包装,食品和饮料及医药行业生产的瓶子,产品油容器、农用化学品容器、健康卫生产品,化妆品产品,和其他一些食品容器。
在设计吹塑工艺时,还有许多因素需要考虑,包括用户(人体工程学),产品(内容,物料,感光性),灌装(颈部、内容和填充线)、包装和表现(例如标签使用和打印)。
成本方面:EBM是最便宜的,IBM的工具通常比EBM贵两倍,而ISBM是最昂贵的。单件生产周期均非常迅速,单套模具生产一批零件只需要1 - 2分钟。实现生产自动化后,劳动力成本可以降到很低。
投产和换模具的成本会比较高,所以机器往往专注于单一产品。
四.计算机在吹塑成型中的应用
通常采用计算机进行吹塑成型设计。对于制品设计和NC程序设计,优先采用三维(3D)系统。对于模具设计更倾向于采用二维(2D)计算机辅助设计系统( CAD)。
促使采用3D CAD系统的是汽车工业。汽车制造商主要用3D技术发展了他们的产品,并让他们的供应商有权使用全部的VDA—FS数据文件¨,。然后模具制造者用这些数据设计模具和对他们的洗削机器编程。
由于制品的复杂性,直接将模型转移到吹塑模具中还无法证明是实际可行的。在大多数情况下,模型是吹塑模具制造中的一个过渡步骤。这可以认为是有用的,因为:在自动化工业中,产品的设计者不是挤出吹塑成型的专家;在真实的生产开始之前,产品经常改变;一个1.l的模型在装配试验中是非常有用的;模具的制造
并不总是很简单,特别是在分型线区域。为了有助于吹塑成型过程及满足模具制造的需要,可能要改变制品。
3D表面数据能够容易地被用于确定参考点以检验制品和对任何测量机器编程。3D CAD设计促使使用人员精确描绘制品的几何形状。另外,用它制作模型是不可能的。
对于包装制品,用3D设计方法确定必要的充模体积,然后反复确定制品的外部尺寸相对较为容易。该方法可减少体积和尺寸的错误,这些错误会导致重复性工作及成本显著提高。
CAD的优点:能够准确描绘制品;消除数据转换引起的错误;容易改变设计,减少主要变化所引起的全部错误;可以抽取任何数据以检查模型、模具和制品的尺寸;快速存取数据。缺点:平面位置模型化( 3D设计)比普通2D设计要贵。
通常,设计所造成成本的增加可通过模型应用时成本的减少得到补偿。