新闻资讯
模具知识培训:塑料模具的失效形式及原因
随着国民经济总量和工业产品技术的不断发展,各行各业对模具的需求量越来越大,技术要求也越来越高,塑料模具的发展是随着塑料工业的发展而发展的。汽车、家电、办公用品、工业电器、建筑材料、电子通信等塑料制品主要用户行业近年来都高位运行,发展迅速,因此,塑料模具也快速发展,我国塑料模具行业日趋大型化。
塑料模具成型的制件表现出它的高精度、高复杂性、高一致性、高生产率和低消耗,塑料模具的加工制造方法有其独特的创造价值,而且塑料制品的种类日益增多,用途不断扩大,制品向精密化、大型化、复杂化发展,成型生产向高速化发展,模具的工作条件也越趋复杂。
一.塑料模具的失效形式
塑料模具主要包括热固性塑料模具和热塑性塑料模具。前者工作温度一般为160~300℃,受力大(300~800MPa),型腔容易产生磨损和腐蚀失效;后者工作温度为150℃以下,承受的工作压力(300~600MPa)和磨损没有前者严重,但部分塑料在加热熔融状态下能够分解出腐蚀性气体,对型腔有较大的压力和腐蚀性。塑料模具的主要失效形式有塑性变形、断裂、表面腐蚀、疲劳和热疲劳、表面磨损失效等。
对于塑料模具的基本失效形式,主要体现以下三个方面:
1.磨损失效
模具在服役时,与成型坯料接触,产生相对运动。由于表面的相对运动,接触表面逐渐失去物质的现象叫磨损。热固性塑料对模具表面的严重摩擦,使模具表面产生划伤(拉毛),影响压制件的外观质量,经多次抛光修复后,因型腔尺寸超差而失效;热固性塑料中含有的固体添加剂也会加剧对模具型腔的磨损,不仅使型腔表面粗糙度值迅速升高,而且还会使模具型腔尺寸超差;当模具选用的材料与热处理不合理,塑料模具的型腔表面硬度较低,也会使模具耐磨性变差,磨损失效可分为以下几种:
(1)疲劳磨损。 两接触表面相对运动时,在循环应力、机械应力与热应力的作用下,使表面金属疲劳脱落的现象,称为疲劳磨损。
(2)气蚀磨损和冲蚀磨损。 金属表面的气泡破裂,产生瞬间的冲击和高温,使模具表面形成微小麻点和凹坑的现象,叫气蚀磨损;液体和固体微小颗粒反复高速冲击模具表面,使模具表面局部材料流失,形成麻点和凹坑的现象,叫冲蚀磨损。
(3)磨蚀磨损。 在摩擦过程中,模具表面和周围介质发生化学或电化学反应,再加上摩擦力的机械作用,引起表面材料脱落的现象,叫磨蚀磨损。其是由于热固性塑料中的固体填料及一些热塑性塑料中存在氯、氟等元素,受热分解析出HCl、HF等强腐蚀性气体,侵蚀模具型腔表面,加剧其磨损失效。表面腐蚀会造成模具型腔表面质量下降及尺寸超差,降低模具寿命。
(4)磨损的交互作用。 摩擦磨损情况很复杂,在一定的工况下,模具与工件(或坯料)相对运动中,磨损一般不只是以一种形式存在,往往是以多种形式并存,并相互影响。
2.断裂失效
模具出现大裂纹或分离为两部分和数部分,丧失服役能力时,称为断裂失效。断裂可分为塑性断裂和脆性断裂。模具材料多为中、高强度钢,断裂形式多为脆性断裂,脆性断裂又可分为一次性断裂和疲劳断裂。
由于塑料模具形状复杂,存在许多棱角、薄壁等部位,在模具工作时易产生应力集中,当这些部位的应力值超过模具材料的断裂强度时,就会发生断裂失效。另外,合金工具钢制作的塑料模具回火不充分时,使用中也容易发生断裂失效。
3.塑性变形失效
塑料模具在服役时,承受了很大的应力,而且不均匀。当模具的某个部位的应力超过了当时温度下模具材料的屈服极限时,就会以晶格滑移、孪晶、晶界滑移等方式产生塑性变形,改变了几何形状或尺寸,而且不能修复再服役时,叫塑性变形失效。塑性变形的失效形式表现为镦粗、弯曲、型腔胀大、塌陷等。
模具的塑性变形是模具金属材料的屈服过程。是否产生塑性变形,起主导作用的是机械、负荷以及模具的室温强度。在高温下服役的模具,是否产生塑性变形,主要取决于模具的工作温度和模具材料的高温强度。
其是指塑料模具在持续受热、受压的作用下,发生局部塑性变形而失效。其原因主要是:所采用模具的材料强度与韧性不足;模具超载使用;模具型腔表面的硬化层过薄,变形抗力不足;模具回火不足;因工作温度高于回火温度而使模具发生软化,从而引起表面起皱、凹陷、麻点、棱角塌陷(堆塌)等。
4.疲劳和热疲劳
塑料模具在工作过程中因承受循环的机械载荷作用,使模具的型腔表面承受脉动拉应力作用,从而引起模具的破坏称为疲劳失效;塑料模具在服役过程中还承受循环的热载荷作用,型腔表面在反复的受热和冷却条件下,可导致模具型腔应力集中处萌生热疲劳裂纹,另外加上模具型腔表面上的脉动拉应力,使热疲劳裂纹向纵深扩展,最终造成模具断裂。
二.影响塑料模具失效的因素
1.结构设计不合理引起失效。
尖锐转角(此处应力集中高于平均应力十倍以上)和过大的截面变化造成的应力集中,常常成为许多模具早期失效的根源。并且在热处理淬火过程中,尖锐转角引起残余拉应力,缩短模具寿命。
2.模具材料质量差引起的失效。
模具材料内部缺陷,如疏松、缩孔、夹杂成分偏析、碳化物分布不均、原表面缺陷(如氧化、脱碳、折叠、疤痕等)影响钢材性能;夹杂物过多引起失效;表面脱碳引起失效;碳化物分布不匀引起失效。
3.模具的机加工不当。
(1)切削中的刀痕。 模具的型腔部位或凸模的圆角部位,在机加工中,常常因进到太深而使局部留下刀痕,造成严重应力集中,当进行淬火处理时,应力集中部位极易产生微裂纹。
(2)电加工引起失效。 模具在进行电加工时,由于放电产生大量的热,将使模具被加工部位加热到很高温度,使组织发生变化,形成所谓电加工异常层。在异常层表面,由于高温发生熔融,然后很快地凝固,该层在显微镜下呈白色,内部有许多微细的裂纹,白色层下的区域发生淬火,叫淬火层,再往里由于热影响减弱,温度不高,只发生回火,称回火层。熔融再凝固层,硬度很高,达610-740HB,厚度约为30μm,淬火层硬度400-500HB,厚度为20μm。回火属高温回火,组织较软,硬度为380-400HB,厚度为10μm。
4.模具热处理工艺不合适。 加热温度的高低、保温时间长短、冷却速度快慢等热处理工艺参数选择不当,都将成为模具失效因素。
(1)加热速度。 塑料模具钢中含有较多的碳和合金元素,导热性差,因此,加热速度不能太快,应缓慢进行,防止模具发生变形和开裂。在空气炉中加热淬火时,为防止氧化和脱碳,采用装箱保护加热,此时升温速度不宜过快,而透热也应较慢。这样,不会产生大的热应力,比较安全。若模具加热速度快,透热快,模具内外产生很大的热应力。如果控制不当,很容易产生变形或裂纹,必须采用余热或减慢升温加速度来预防。
(2)氧化和脱碳的影响。 模具淬火是在高温度下进行的,如不严格控制,表面很易氧化和脱碳。另外,模具表面脱碳后,由于内外层组织差异,冷却中出现较大的组织应力,导致淬火裂纹。
实例
T10A钢线圈架塑料压注模的失效分析
(1)工作条件与加工流程
塑料压注模(见图2)工作压力在250MPa以上,工作温度高于200℃。模具材料为T10A,其加工流程为:下料→锻造→球化退火→切削加工→淬火 + 低温回火→磨削加工→抛光→装配等。模具热处理后的硬度为60~62HRC。
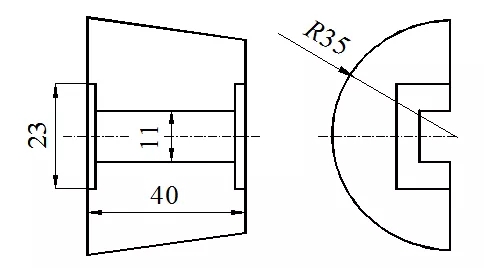
图2 线圈架塑料压注模简图
(2)失效分析
该模具寿命在2000件以下,其主要的失效形式为型腔表面拉毛(划伤)和棱边塌陷等。对失效模具进行硬度检测发现,型腔表面与棱边处的硬度为56~58HRC,表明模具在使用过程中有一定的硬度降低,其金相组织为回火马氏体 +粒状渗碳体 +少量残留奥氏体。
通过对模具的硬度降低分析来看,模具的服役温度高于回火温度(200℃),同时也与模具的回火不足有关,其使模具在服役过程中受热后继续回火,导致马氏体的分解与残留奥氏体的转变,在压力作用下产生“相变超塑性”流动,引起模具型腔表面拉毛与棱边的塌陷。
(3)对策与效果
1)适当提高模具的最终回火温度,如采用250~270℃回火,即高于模具的工作温度(200℃)。同时,增加回火保温时间。
2)采用两段回火工艺。在保证模具较高的硬度的前提下改善材料的韧性,采用两段回火工艺:200℃ × 1.5h × 1次 +260℃ × 1.5h × 1次,模具表面硬度为56~58HRC,模具寿命可达1.8万件。