新闻资讯
模具材料对铝合金压铸模热平衡影响的有限元研究
铝合金压铸模的主要失效形式为热疲劳。 铝 合金的熔化温度为 600~760℃ ,其压铸模型腔表面 温度高达 600℃ 以上,热疲劳失效约占 70%。 热 疲劳主要是由于在压铸循环中, 热应力大于热疲劳 强度极限。而热应力又是由压铸模温度波动导致的。 所以摸清铝合金压铸循环过程中压铸模温度的演化 规律以及热平衡的形成就变得越来越重要。赵信毅、 Hsieh 、李朝霞、张光明等人分别研究了冷却工艺、冷 却水温及冷却管径、模具预热温度、浇注温度等因素 对镁合金及铝合金铸件和模具温度场的影响。 但 是模具材料对热平衡影响的未见报道, 而模具材料 对铝合金压铸模温度、 热平衡以及使用寿命有非常重要的影响。
本文采用 PRO/E 和 PROCAST 软件,以前盖铝 合金压铸件为例, 通过对其压铸循环过程中温度场 的模拟,研究压铸模的热平衡的形成,模具材料对距 模具型腔表面不同位置点的温度曲线的影响, 分析 模具材料对热平衡形成规律的影响, 为选定合理的 模具材料提供指导。
1 模型的建立及参数设置
1.1 模型的建立
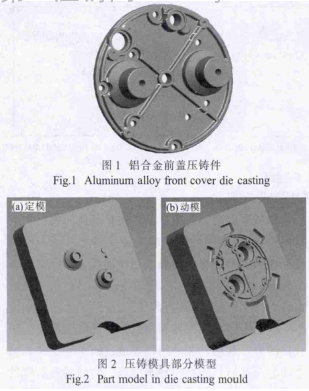
图 1 为前盖铝合金零件图, 其材质为 A390 铝 合金。 图 2 为定动模部分简化模型。
1.2 参数设置
动定模的预热温度为200℃,浇注温度为700℃ ,铸件与模具的换热系数为1500W/(m2·C),模具间的换热系数为1000W/(m2·C) ,模具与空气的换 热系数为5W/(m2·C),模具与脱模剂的换热系数为500W/(m2·C)。 由于金属液瞬间充满型腔,与此同时本模拟重点考虑是模具,故不考虑充型过程。循环周 期为30s,第0s开始充型,第15s开模,第20s推出 压铸件,第23s喷脱模剂,第25s喷涂结束,第29s合模。
1.3 物性参数
模具材料采用性能差别大的 H13 、陶瓷和纯铜。 影响模具温度的主要因素为模具材料的热导率和比 热容。 图 3 为模具材料的热导率。
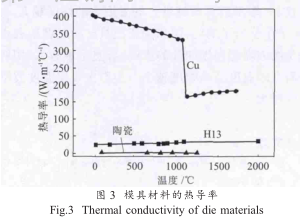
2 模拟结果及分析
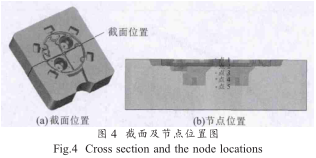
选取动模中间截面上的5个节点为分析对象。 图4为截面位置及节点位置图。节点1~5分别代表 图4(b)中从上到下的5个点。节点1在型腔表面,节点5离型腔表面距离最远。
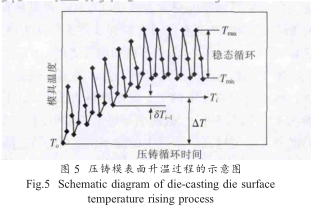
图5为压铸模从预热温度To到稳态的升温示 意图。 压铸模从第 1 个压铸循环前的平均的预热 温度To增加到稳态的温度Tmin 。从图5可以得到,任 意一个压铸循环开始时模具上某点的温度(Ti) ,在达 到稳态前可以表示为模具预热温度与该压铸循环前 经历的每一个压铸循环的温度增量(δT)之和:
T i =δT i-1 +δT i-2 +δT i-3 + …… +T 0 =T 0 +ΔT (1)
压铸模内各点温度的变化通过连续的压铸模拟来实 现,每一次工作循环都是冷却、开模、喷脱模剂、合模 几个阶段构成。将上述温度场的模拟过程继续下去, 达到热平衡时 T max 和 T min 保持为常数, 每次压铸循 环温度增量 (δT) 为零。
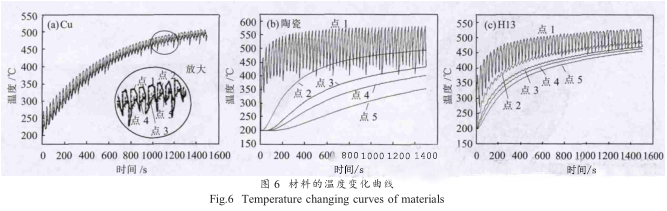
图 6 为 H13 、 铜和陶瓷模具材料连续压铸时 5 节点温度变化曲线。从图 6 中可以看出,模具温度从 预热温度 200℃ 经过大约 50 个压铸循环,压铸模具 温度变化趋于稳定,压铸模进入热平衡状态。在这个 热平衡形成过程中,随着循环的进行,模具表面的 5 个节点的温度每循环一次整体温度提高 δT 不尽完 全相同,开始压铸循环时 δT 值最大,随着压铸次数 增加, δT 越来越小,当达到热平衡后 δT 为零。 距型 腔表面最近的节点 1 每次循环的温度波动 (T max -T min ) 最大。离型腔表面越远的节点温度波动越小。图 6(a) 中 5 个节点的温度波动差别不大, 最重要原因是铜的导热系数很大, 导致温度从型腔表面向基体或从 基体向表面传递很快,所以温度波动厚度比较大。图 6(b) 中陶瓷模具材料的 5 个点只有节点 1 有温度波 动,其它 4 个节点在每个循环基本没有温度波动。这 主要是由于陶瓷的热导率很低, 每次压铸循环温度 变化深入的模具厚度很薄。 图 6(c) 的 H13 模具材料 的 1~4 节点温度都有波动, 只有节点 5 没有波动。 这是由于 H13 的热导率介于铜和陶瓷之间。
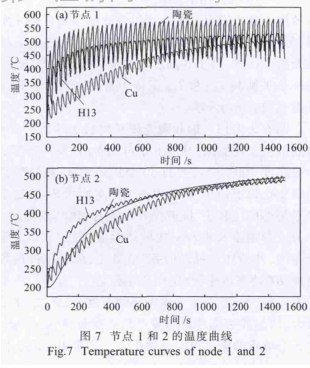
图 7 (a) 为三种模具材料节点 1 的温度变化曲 线。 热平衡后节点 1 的 T max 陶瓷材料为 582℃ , H13 为 529℃ ,铜为 506℃ 。这说明导热系数越小,型腔表 面点最大温度越高。 节点 1 的波动幅度 (T max -T min ) 陶 瓷材料为 142℃ , H13 为 64℃ ,铜为 43℃ 。 型腔表面 点的温度波动幅度陶瓷材料最大, H13 次之, 铜最 小。 这说明型腔表面在吸热和散热时, 导热系数越小热量从型腔表面向模具基体或从基体向表面扩散 越困难,表面点温度波动幅度也就越大。 图 7(b) 为 三种模具材料节点 2 的温度变化曲线。 节点 2 在型 腔内部,离型腔表面一定距离。三种模具材料的型腔 次表面的温度波动幅度比型腔表面的温度波动幅度 小。 这是由于次表面不和高温铝以及低温的脱模剂 直接接触。 其吸热和散热都要通过该点到型腔表面 之间的模具材料的热传导来完成。 所以其对温度的 敏感性比型腔表面弱。 在次表面点 2 铜的波动幅度 最大, H13 次之,陶瓷材料最小。 这是由各种材料导 热系数所决定的。
3 结论
(1) 利用 PRO/E 和 PROCAST 建立了前盖铝合 金压铸的三维有限元模型。
(2) 分析了距型腔表面不同距离的 5 个节点的 温度变化曲线。指出 50 次压铸循环后模具进入热平 衡状态。距型腔表面越近点的温度波动幅度越大。
(3) 分析了 H13 、铜和陶瓷模具材料对型腔表面 点及次表面层温度曲线的影响。导热系数越大,型腔 表面点的温度波动幅度越小, 型腔次表层温度波动 幅度越大。