新闻资讯
「技术干货」铝合金车体压铸结构件成型工艺控制要素的剖析
「技术干货」铝合金车体压铸结构件控制要素的剖析
一、压铸工艺概述
在美国特斯拉新能源汽车推出以前,德国斯图加特汽车研发中心及莱茵公司就有关铝合金压铸结构件的材料和工艺等方面进行了有效的研发工作,并在相关的车型上得到了应用。
新能源汽车的推出,导致了一场对传统燃油汽车的革命,并预示着汽车智能化开启的前景………,而车体压铸结构件的推出将进一步拓展铝合金压铸产品的应用空间,对汽车轻量化将产生深远影响。
从传统燃油汽车向新能源汽车转型的变革中,车体结构件采用铝合金压铸整体结构紧凑,刚性增强,重量得到减轻,这些优势得到体现,但要实现这种技术转型和变革,许多技术要素尚要认真剖析和讨论
二、车体压铸结构件的控制要素
1、车体结构件产品设计图与压铸铸件图的协调,产品图涉及的合金材料选材,关系到铸造工艺性及其合理可行性,按ASTMB85铝合金技术标准中对压铸合金的压铸特性应进行评估,对结构件重要部位的应力负荷区域要标示清楚,以备进行压铸件切取试样检验提供依据,以保证结构件质量,如此这些是以往常规铝合金压铸少见的。
2、结构件压铸模设计与制造、浇排系统设计及模流分析
压铸模的工艺设计、浇排系统的设计,模具冷却及加热系统的热平衡布局以及关键的浇口截面与比例的设计等技术方案要合理可行,并保证产品高应力区的质量,必要时可适当提高按投影面积选择压机锁模力的吨位以及真空压铸能力。
3、压铸结构件的合金选材
压铸结构件一般力学性能的高塑性要求是突出特点,而选择合金化学成分既要考虑性能,也要兼顾压铸件成型要求和壁厚均匀程度,欧洲已进行的压铸结构件合金选材工作,大致归纳为下表:
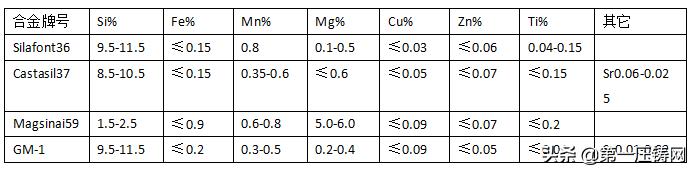
我们试制研制的是GM-1组化学成分
其力学性能要求:抗拉强度≥250Mpa,延伸率≥10%,根据性能要求,结合GM-1化学成分组成和其产品图的结构件特点进行了多组分的分炉分批次的试制测试。选择接近共晶成分的硅元素是满足该压铸产品的壁薄、形状复杂的成型需要,加入硅的另一特点是新近显微研究分析表明,在铸件凝固过程中,硅元素产生膨胀,减少了收缩,并且与其他元素产生的热裂倾向达到平衡作用,对铸造应力也有一定抑制。但是硅元素降低液态合金中氢气溶解度,以至含硅较高特别是接近共晶成分的含硅合金孔洞缺陷是最大弊端。严格控制铁含量是高塑性能所必需的,至于压铸件粘模问题,外加适当的锰可以起到类似的作用。以下就有关诸元素的金相图谱示意,它们在合金中的作用加以解读,就压铸铝合金而言,添加Cu或Mg是通常的基体强化元素,即相应形成Al2Cu或Mg2Si强化相,通过压铸过程中的激冷使其部分固溶强化,而对压铸件采用T1时效处理,其也对固溶部分产生析出硬化而实现性能的提高。
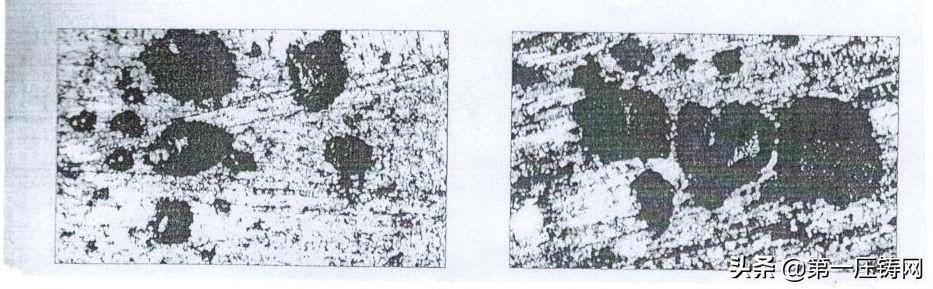
图1:共晶AL-SI类合金的孔洞典型缺陷
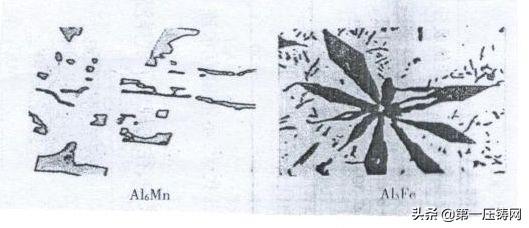
图2:压铸铝合金中AL3Fe\AL6Mn化合物
高塑性压铸铝合金虽然高速冷却速度可以抑制AL3Fe长大,但它的针状组织形态对高塑性是致命的,故采用加Mn形成方块的AL、Mn化合物代替铁实践证明是有效可行的。
锶的长效和对压铸共晶Al-Si类合金的变质是有效的,虽然它有吸氢倾向,但可在合金的强化净化工艺中解决。
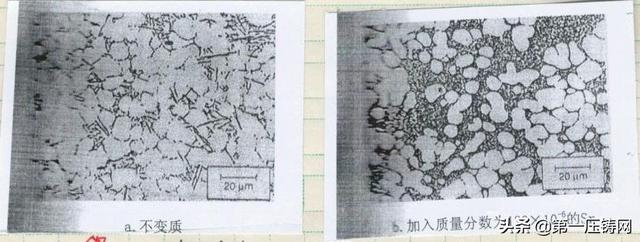
图3:锶的变质效果对比
从图3的锶的变质效果看出这种变质后共晶硅的形态是高塑性所盼求的。
4、合金熔炼与净化
由于车体压铸结构件对力学性能的要求,决定了它必须通过热处理来实现,而压铸件的热处理特别是固溶处理,对合金的净化和真空压铸是有特殊要求的,故对车体结构件合金液处理既要除气同时也要除渣,必要时尚需加熔剂处理。试验表明,铝液中AL2O3的夹渣对精炼中的氢气有极强的吸附作用,将形成吸附核心,使其难于去除,净化处理的目的就是兼顾其双重作用,净化处理的下图装置时间证明是有效的。
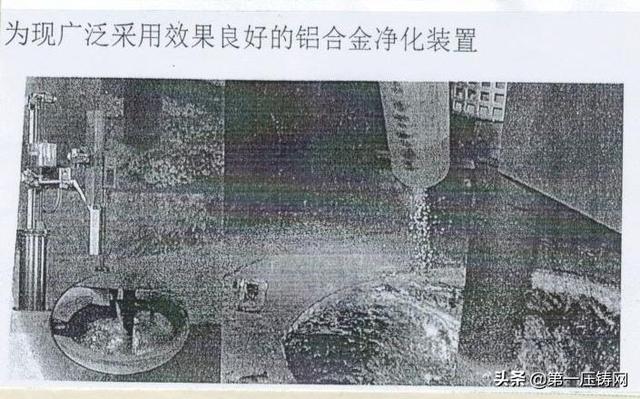
5、真空压铸
鉴于车体结构件性能的特殊要求,以及压铸件的结构特点,对车体结构件一般采用真空压铸,而采用专用的真空压铸机实践证明是最佳选择,如德籍的富莱真空压铸机反映良好,真空压铸机可将经净化良好的合金液压铸成基本无缺陷的产品,当然其中参数的优化和模具的设计制造的准备及涂料喷涂等都要与其相适应。真空压铸件的质量好坏与热处理最后性能密切相关。压铸机锁模力吨位选择,可按车体结构件重要性优化,必要时可按一般投影面积选择高一级别的机型。确保结构件质量安全。
6、热处理
对于铝合金车体结构件的热处理,至目前知道的信息表明,国内外一般采用的是固溶处理加高温时效,即是T7处理,笔者主编的国家军标GJB1695铸造铝合金热处理规范中对T7热处理规范有专门的列述,它是国防科工委批准颁发的,由国家航空工业多家企业验证,我们在和GM公司总冶金师讨论沟通中也得到认可,实践中也得到验证,对保证合金的高塑性是可行的。
需指出的是,固溶处理和高温时效规范的确定视合金成分和压铸件具体情况而定,包括处理的温度保温时间亦如此,具体规范可参照GJB1695有关合金系列进行。
综上对车体压铸结构件控制要素的剖析,涉及的工艺要点颇多,仅是对已实践的归纳,很难以概论全,不少论点尚值得商榷和进一步验证。
三、讨论:
1、车体压铸结构件取代的是原变形铝的部分型材板材,比较多的是冲压件、铆接和焊接件,虽从车体整体结构紧凑,刚性和减轻重量方面优势明显,但从结构件的设计安全系数,使用寿命以及对现有压铸操作手段全面衡量起来尚有完善之处,特别是对压铸件的质量偶然性和内部质量的不稳定怎么防患于未然,尚值得进一步深究。
2、建立健全相关对车体压铸结构件的检验手段,包括对现有常规手段的细化,深化,特别是通过定期抽检设计指定部位的切取样件的性能测试,通过稳定工艺和过程控制来实现压铸件质量稳定等。
3、严格铝合金结构件试制与定型的评估,设计与工艺的评估,必要时对关键结构件要执行会签制度,这在航空工业中有较成功的先例和成熟的经验可以参考。
4、对于外贸的相关压铸结构件,可以通过客户的质量要求,提高相应的检验级别,条件不充分的创造条件,以外促内,提升压铸件质量水平,适应外贸市场需求。
5、实行以企业为中心的产校研结合的研发体制是可行的,特别是企业研发力量薄弱的情况下更是最佳选择。
6、近期,对讨论比较多的共晶Al-Si合金中强化元素是否可以叠加的问题,笔者的看法是:就目前国内外压铸铝合金的应用现状而言,除过共晶Al-Si之外,如美国的390或日本的ADC14及我国的YL-117等过共晶AL-Si合金,它们的共同特点是将强化元素Cu和Mg同时叠加加入的,这是基于过共晶的Si的共晶组织可以包容其强化相的共存,但对这类合金必须有相应加磷变质手段,以及相应的浇铸工艺控制措施,以抑制初晶Si粗大组织出现而给机加工造成困难。