新闻资讯
【压铸模设计贴】客户对铸件表面粘模缺陷不满意,如何改善?
随着市场竞争的不断加大,很多主机厂商向零部件商提出了高规格要求,仅铸件结构强度上的合格很难满足客户需求,铸件表面质量至关重要,它不仅影响零件外观,过多的表面缺陷更直接影响铸件气密问题。压铸件表面粘模缺陷造成的原因有哪些?如何去改善这些问题?
粘模成因有哪些?
01.界面反应
铝合金对铁有很强的亲和力,铝液在和模具接触时,会产生一种铝合金和模具材料的化合物,铝液或模具温度越高,原子的热振动就越激烈,铝液对模具的腐蚀变得越来越大 ,最终在模具表面形成了粘模区,出现粘模后,工人用打磨工具清理,这样模具上的的氮化层极易遭到破坏,模具腐蚀更快,粘模现象更为激烈。
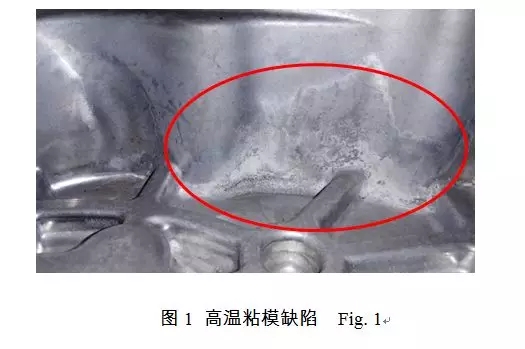
02. 模具设计
外部结构引起粘模
铸件粘模大多是由于模具结构设计原因 或后续处理不当 造成的。模具表面渗氮或碳氮共渗热处理目的是获得更高的表面硬度和耐磨性,如果热处理不充分 导致氮化层过薄或不均,或人为打磨 导致氮化层破坏造成型壁表面粗糙会造成粘模;另外,模具拔模斜度过小;型芯或者型壁出现反斜度现象;浇注系统设计不合理,铝液直接冲刷型壁或者型芯 ,这些也是引起粘模的原因。
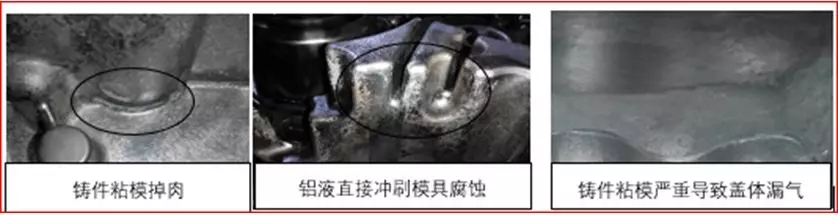
内部结构引起的粘模
模具设计过程中冷却水道有盲区,通常自来水压力(≤4bar)无法冷却>25mm的模厚,因此出现局部高温 ,产生粘模现象;高温铝水对浇口的冲刷最严重,该处若得不到及时冷却,很容易造成分流锥或浇口附近本体腐蚀,造成严重粘模,图3所示。
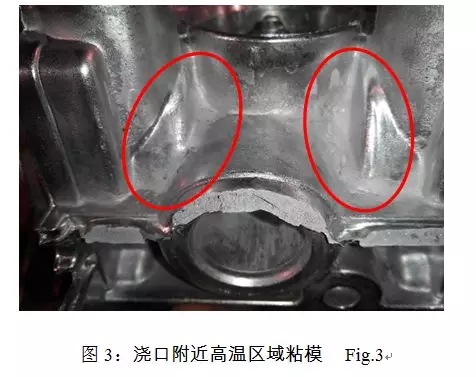
03. 脱模剂的作用
脱模剂与模具直接接触,它在金属液和模具之间形成一层致密的隔离层,保证金属液冷却后能顺利脱模。若要降低铸件粘模缺陷,在其他工艺条件都一致的前提下,脱模剂质量好坏就显得尤为重要。
热重分析(Thermogravimetric Analysis,TG或TGA)显示,当温度在200℃~400℃范围时,随着温度的升高,曲线斜率最大,这时候脱模剂成分损失最严重,模温最佳温度范围在200℃~300℃,既保证金属液有较好的流动性,又充分发挥了脱模剂的润滑性能。
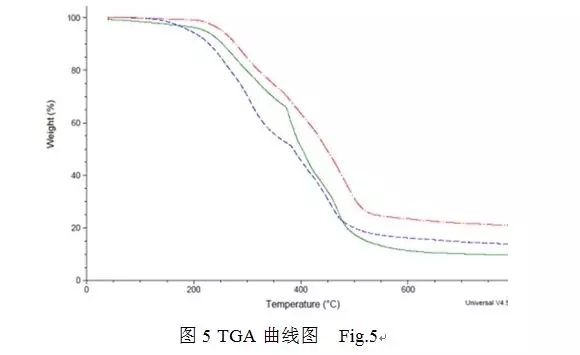
优质的脱模剂需要保证水基溶液里的稀释剂能很快地挥发掉,不增加型腔内气体; 与模具亲和力强,并不产生堆积,保证涂覆均匀;对模具及铸件不产生腐蚀作用; 破乳效果良好,COD排放值抵,降低环境污染源……
04. 压铸设备及工艺参数
高速压射 可以大大提高铸件充型能力,但往往带来其他不利缺陷,比如飞边。飞边往往不仅造成铸件清理困难,铸件尺寸超出规定范围,模具滑块进铝导致清理困难等问题,同时加剧了金属液与模具的结合力,加大了粘模现象,大大缩短了模具和压铸机的寿命。
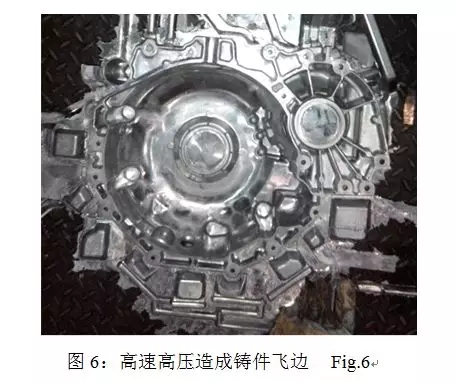
如何改善粘模缺陷?
1. 合理降低模具温度
温度越高,铝液和模具亲和力越强,粘模现象越明显。统一喷涂、工艺参数不变前提下,将浇口附近易粘模位置对应的水阀采取关闭、半开、全开3种状态各生产50件去试验,得出结果如下表:

模具正常生产后,温度很快就达到200℃以上,不必担心模具温度过低导致脱模剂涂覆性能,因此尽量开启冷却水管,降低模具温度,进而降低铝-铁界面反应和提高脱模剂附着力 。
2. 脱模剂的选取和喷涂方式
降低铸件粘模缺陷另一重要的辅料就是脱模剂。良好的脱模剂不仅有较好的脱模作用,而且还能在模具上形成一层保护层,长期生产后浸渗模具表面,降低金属液的浸蚀。
喷涂方式对产品粘模也非常重要,待模具温度降低至200℃~250℃时,大量的脱模剂有效成分才能涂覆在模具表面 。脱模剂最好的喷涂方式就是雾化方式实现来回喷涂 ,这样保证脱模剂有充分的时间附着模具表面。
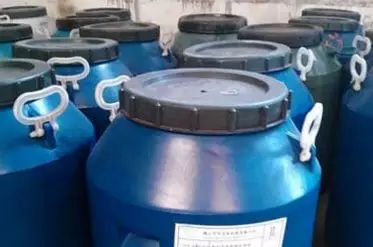
3. 保证质量下,降低高速和铸造压力
铸件的缩孔、气孔等缺陷不一定只有增加压力或速度才能解决,一味的加大压力不仅会增加粘模几率,而且将大大降低模具和设备寿命 ,出现缩孔时,查找原因,是否是铸造压力不够造成的,检查氮气瓶压力表是否合适,铝液光谱和密度当量是否在工艺要求范围等……
4. 模具的维护保养 粘模对生产和质量都有着很大的影响,合理的浇道设计,保证产品质量前提下尽量低模温(模温也不能太低,否则会增大抱紧力和出现产品冷隔缺陷)、低铝温、低高速、低高压生产,局部粘模需要铝抛光磨头打磨或硬度较低的金属铲除,防止模具氮化层破坏;选择良好的脱模剂性能和合理的喷涂工艺等才能保证质量。 对已氮化过的模具,抛光要慎重,防止破坏表面的氮化层 ,防止越抛光越粘模的情况;对于内浇道冲击部位或型芯,可以使用碳化钨棒涂覆机 ,对模具表面以电火花型冶金方式喷涂碳化钨微颗粒层,金属钨微粒与基体金属结合不会脱落,能提高模具表面的抗粘模性。
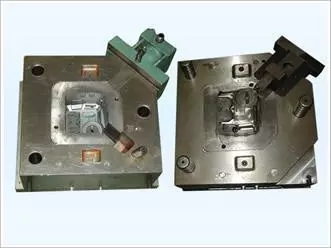
粘模对生产和质量都有着很大的影响,合理的浇道设计,保证产品质量前提下尽量低模温(模温也不能太低,否则会增大抱紧力和出现产品冷隔缺陷)、低铝温、低高速、低高压生产,局部粘模需要铝抛光磨头打磨或硬度较低的金属铲除,防止模具氮化层破坏;选择良好的脱模剂性能和合理的喷涂工艺等才能保证质量。